Understanding the cost of CNC milling services: What you need to know
By:Admin
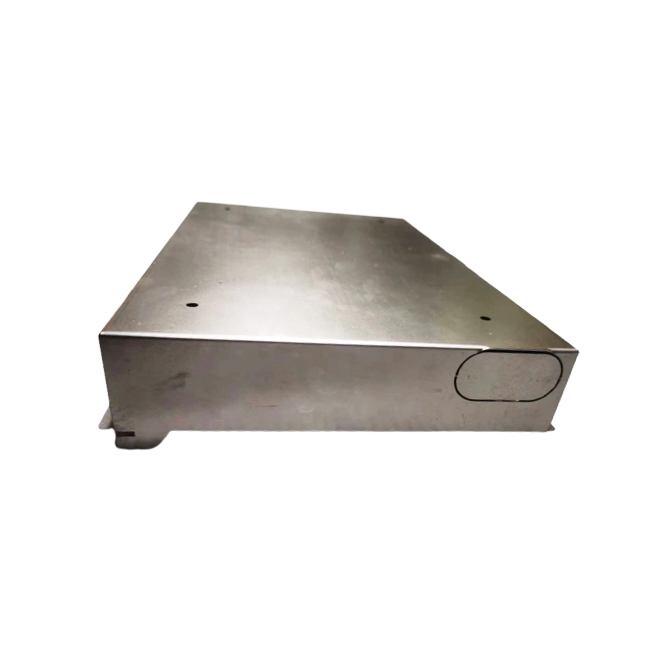
CNC milling is a subtractive manufacturing process that uses computer numerical control (CNC) machines to remove material from a workpiece to create a custom-designed part or product. This process is widely used in various industries, including automotive, aerospace, electronics, and more. With the increasing demand for precision-engineered components, companies are constantly looking for reliable and cost-effective CNC milling services.
[Company Name] understands the importance of providing high-quality CNC milling services at a competitive price point. With state-of-the-art CNC milling machines and a team of skilled technicians, the company is able to deliver precise and complex parts with fast turnaround times. This combination of advanced technology and expertise allows [Company Name] to offer cost-effective solutions to its clients without compromising on quality.
One of the key factors that contribute to the cost-effectiveness of [Company Name]'s CNC milling services is its efficient use of materials. By optimizing the cutting process and minimizing material waste, the company is able to reduce production costs and pass on the savings to its clients. This not only makes [Company Name]'s services more affordable but also contributes to a greener and more sustainable manufacturing process.
In addition to its competitive pricing, [Company Name] prides itself on its dedication to customer satisfaction. The company works closely with its clients to understand their specific requirements and provide tailored solutions that meet their needs. Whether it's a small batch of custom components or a large-scale production run, [Company Name] is committed to delivering high-quality CNC milling services that exceed expectations.
The company's commitment to excellence and cost-effectiveness has earned it a strong reputation in the manufacturing industry. With a track record of delivering precision-engineered components to a diverse range of clients, [Company Name] has established itself as a trusted partner for companies looking for reliable CNC milling services.
As the demand for CNC milling continues to grow, [Company Name] is well-positioned to meet the needs of its clients with its cost-effective solutions. The company's ongoing investment in technology and expertise ensures that it stays ahead of the curve and continues to deliver exceptional value to its clients.
In conclusion, [Company Name] is setting a new standard for cost-effective CNC milling services. With its advanced technology, skilled workforce, and dedication to customer satisfaction, the company is revolutionizing the industry and providing clients with high-quality, precision-engineered components at a competitive price point. As the manufacturing industry continues to evolve, [Company Name] remains at the forefront, leading the way with its innovative approach to CNC milling.
Company News & Blog
Revolutionary Metal Printing Services: Unlocking New Possibilities for Advanced Printing Technology
Title: Advancements in Metal Printing Services Revolutionize Manufacturing IndustryIntroduction:In a bid to cater to the growing demand for innovative manufacturing solutions, the metal printing service industry has witnessed rapid advancements. Through cutting-edge technology and intricate design capabilities, metal printing services are reshaping traditional manufacturing processes, allowing for faster production, enhanced precision, and greater customization options. This article explores the evolution of metal printing services and highlights their transformative potential for numerous industries.1. Historical Background:Metal printing services have a rich history that dates back several decades. Initially, the technology was limited to prototypes and small-scale production due to cost and complexity constraints. However, recent breakthroughs have made metal printing services more accessible, economical, and scalable. Today, companies like (brand name) are utilizing advanced metal printing techniques to cater to a wide range of industries, including aerospace, automotive, healthcare, and consumer goods.2. Advantages of Metal Printing Services:Metal printing services offer several advantages over traditional manufacturing techniques, making them an attractive option for businesses seeking innovation. First, the ability to create complex geometric shapes with unparalleled precision ensures consistency and accuracy in the final product. Second, metal printing services provide an opportunity to reduce waste material, as only the necessary metal is used during production. This eco-friendly approach aligns with sustainable manufacturing practices.3. Industry Applications:The versatility of metal printing services has resulted in its adoption across numerous industries. In the aerospace sector, metal printing has revolutionized the production of engine parts, reducing weight while maintaining strength and performance. Automotive manufacturers are utilizing metal printing services for prototyping, customizing designs, and manufacturing lightweight components that improve fuel efficiency. Moreover, the healthcare industry is benefiting from metal printing by creating patient-specific implants and prosthetics with optimal fit and functionality.4. Enhanced Material Options:With technological advancements, metal printing services have expanded beyond traditional metals such as steel and aluminum. Today, (brand name) and other companies offer a wide range of material options, including titanium, cobalt-chrome, nickel alloys, and even precious metals like gold and silver. This flexibility enables the production of unique and specialized products tailored to specific industry requirements.5. Increased Design Freedom:One of the most significant advantages of metal printing services is the freedom it provides in design. Complex and intricate designs, previously difficult or impossible to produce, can now be realized with ease. Metal printing services allow for the amalgamation of multiple parts into a single assembly, reducing assembly time and eliminating the need for traditional joining techniques. This streamlined process not only saves time but also reduces production costs.6. Customization and Personalization:Metal printing services offer customization opportunities that were previously unimaginable. Companies can create personalized products, tailor-made to meet the unique preferences and requirements of individual customers. From jewelry and fashion accessories to intricate architectural components, metal printing services allow for intricate designs with personalized touches.7. Future Implications:The rapid advancements and increasing accessibility of metal printing services suggest a promising future for the manufacturing industry. As technologies continue to evolve, the scope for innovation and creativity in design will only expand further. Furthermore, the adoption of metal printing services may lead to supply chain optimization, reduced manufacturing lead times, and increased collaboration between designers and manufacturers.Conclusion:The increasing demand for efficient, precise, and sustainable manufacturing has accelerated the growth of metal printing services. With the ability to produce intricate designs, reduce waste, and offer customization options, metal printing services have revolutionized numerous industries. The pioneering efforts of companies such as (brand name) are redefining the manufacturing landscape, ushering in a new era of possibilities for businesses seeking to stay ahead in the competitive market.
Innovative 3D Printed Prototype Designs: Advancements in Technology
[Company Name], a leading innovator in the field of 3D printing technology, has recently unveiled a groundbreaking new prototype design that is set to revolutionize the industry.The new prototype, which has been in development for over a year, represents a major leap forward in 3D printing technology. It is the result of a collaboration between [Company Name]'s team of engineers and designers, who have pushed the boundaries of what is possible with 3D printing.The prototype design, which has not yet been named, incorporates a number of innovative features that set it apart from other 3D printers on the market. One of the key innovations is the use of advanced materials that allow for greater precision and detail in the printed objects. This makes the prototype ideal for a wide range of applications, from prototyping and design to manufacturing and production.In addition to its advanced materials, the prototype also boasts a number of unique capabilities that make it easier to use and more versatile than other 3D printers. For example, it has a larger build volume, allowing for the creation of larger objects, and a more intuitive user interface that makes it easier for users to create and customize their designs.The unveiling of the prototype design marks a significant milestone for [Company Name], which has been a pioneer in the field of 3D printing since its founding. The company has a long history of pushing the boundaries of what is possible with 3D printing, and the new prototype is a testament to its ongoing commitment to innovation and excellence.In addition to its groundbreaking prototype design, [Company Name] is also known for its commitment to sustainability and social responsibility. The company has made significant investments in sustainable production methods and has worked to reduce its environmental impact. It has also been involved in a number of initiatives aimed at using 3D printing technology to create affordable housing and medical supplies for communities in need.Looking ahead, [Company Name] has ambitious plans for the future. It is already in talks with a number of potential partners and customers who are interested in the new prototype design, and it is confident that it will be able to bring the prototype to market in the near future. The company also has plans to continue pushing the boundaries of what is possible with 3D printing, and it is committed to remaining at the forefront of technological innovation in the field.The unveiling of [Company Name]'s new prototype design is sure to be a major event in the world of 3D printing. With its advanced materials, unique capabilities, and commitment to sustainability, the prototype represents a major leap forward for the industry. As [Company Name] continues to work towards bringing the prototype to market, it is clear that the company's dedication to innovation and excellence will ensure its continued success in the years to come.
Transform Your Designs with Vacuum Casting 3D Printing Technologies
Vacuum Casting 3D Printing revolutionizes the Manufacturing Industry[Date], [City] - The manufacturing industry has taken a giant leap forward with the introduction of Vacuum Casting 3D Printing technology. This revolutionary process, which combines the precision of 3D printing with the efficiency of vacuum casting, has opened up a whole new realm of possibilities for product development and production.[Company Name], a leader in advanced manufacturing solutions, has been at the forefront of this technology, reshaping the manufacturing landscape. With their innovative processes and cutting-edge equipment, they have successfully helped numerous companies overcome traditional manufacturing limitations, providing cost-effective and time-efficient solutions.Traditional manufacturing methods often come with significant limitations, including high production costs, long lead times, and limited design flexibility. However, Vacuum Casting 3D Printing offers a game-changing alternative. By utilizing a combination of 3D printing and vacuum casting, [Company Name] has been able to overcome these constraints, providing businesses with a streamlined manufacturing process.One of the key advantages of Vacuum Casting 3D Printing is its ability to produce highly complex and intricate designs that were previously difficult or impossible to achieve using conventional manufacturing methods. The process starts by creating a 3D printed mold, which is then used to produce a silicone mold through vacuum casting. This mold can then be used to create multiple copies of the original design, even with undercuts, intricate details, and delicate features. This provides manufacturers with the freedom to create complex parts that meet the strictest of demands.Another major benefit of Vacuum Casting 3D Printing is its cost-effectiveness, especially when compared to traditional manufacturing methods. The process eliminates the need for expensive tooling, molds, and machining setups, reducing overall production costs significantly. This not only makes it an attractive option for small and medium-sized enterprises but also enables larger companies to optimize their production processes by reducing costs and increasing efficiency.Speed is another remarkable advantage of Vacuum Casting 3D Printing. With traditional manufacturing, developing and producing a new product can take weeks or even months. However, the Vacuum Casting 3D Printing process drastically reduces lead times, enabling rapid prototyping and iterative design improvements. This allows companies to bring products to market faster, giving them a competitive edge in today's fast-paced business environment.[Company Name] has spearheaded the adoption of Vacuum Casting 3D Printing across various industries, including automotive, aerospace, consumer electronics, and medical devices. Their team of experts works closely with clients to understand their specific manufacturing needs, and they provide tailor-made solutions to optimize the production process. By combining their expertise in materials selection, 3D printing, and vacuum casting, [Company Name] ensures that clients receive the highest quality products with exceptional speed and accuracy."Our Vacuum Casting 3D Printing technology has revolutionized the way companies manufacture products," said [Company Spokesperson]. "We are proud to be helping businesses break free from the limitations of traditional manufacturing and embrace a more agile and efficient approach. With our expertise and state-of-the-art equipment, we are committed to driving innovation and delivering results that exceed our clients' expectations."The introduction of Vacuum Casting 3D Printing technology by [Company Name] has created ripples in the manufacturing industry. By addressing the limitations of traditional manufacturing methods, this innovative process offers a cost-effective and time-efficient alternative that unlocks new possibilities for product development and production. With such advancements, manufacturers can now bring their ideas to life more easily and faster than ever before, ushering in a new era of manufacturing excellence.
High-Quality Brass Parts Fabrication Services: Custom Brass Parts Manufacturing for Various Applications
[Company Name], a leading manufacturer of precision engineered components, has recently announced the production of a new fabrication brass part for a wide range of industrial applications. The company has utilized its decades of expertise and state-of-the-art technology to develop this high-quality component that is set to meet the needs of various industries.The fabrication brass part, which has been developed using advanced machining processes, is a testament to [Company Name]'s commitment to innovation and excellence in the manufacturing sector. With a focus on meeting the rapidly evolving needs of its customers, the company has successfully created a component that offers superior performance and durability.The new fabrication brass part is designed to cater to the needs of industries such as automotive, aerospace, and electronics, among others. With its excellent corrosion resistance and electrical conductivity, the part is set to become an essential component in a wide range of applications. Whether it is used in automotive components, electrical connectors, or precision instruments, this fabrication brass part is expected to deliver exceptional performance under diverse operating conditions.[Company Name] has always been at the forefront of manufacturing precision engineered components, and the development of this fabrication brass part further solidifies its position as an industry leader. The company has a long-standing reputation for producing high-quality components that meet the stringent requirements of its customers. With a strong focus on research and development, [Company Name] has consistently delivered innovative solutions that have contributed to the advancement of various industries.The production of the fabrication brass part is a testament to [Company Name]'s dedication to providing its customers with cutting-edge solutions that address their specific needs. By leveraging its extensive manufacturing capabilities and technical know-how, the company has been able to develop a component that offers unmatched performance and reliability. Furthermore, [Company Name] prides itself on its ability to customize products according to the unique requirements of its clients, ensuring that the fabrication brass part meets the exact specifications of each application.In addition to its commitment to delivering high-quality products, [Company Name] also places a strong emphasis on environmental sustainability and corporate responsibility. The company has implemented stringent measures to minimize its environmental footprint and ensure that its manufacturing processes are in line with the highest industry standards. By adhering to strict quality control protocols, [Company Name] has maintained a reputation for producing components that not only meet performance requirements but also adhere to stringent environmental and safety regulations.The introduction of the fabrication brass part is a significant milestone for [Company Name], as it represents the company's ongoing efforts to diversify its product portfolio and cater to a broader range of industries. By continuously investing in research and development, [Company Name] has been able to stay ahead of the curve and meet the evolving needs of its customers. The company remains dedicated to remaining at the forefront of the manufacturing sector, and the production of the fabrication brass part is a testament to its unwavering commitment to excellence.With its extensive expertise, state-of-the-art technology, and unwavering dedication to delivering superior products, [Company Name] is poised to make a significant impact with the introduction of the new fabrication brass part. As the company continues to expand its capabilities and reach, its innovative solutions are set to play a crucial role in driving the advancement of various industries. [Company Name]'s commitment to excellence and innovation ensures that it remains a trusted partner for companies seeking high-quality, precision-engineered components.
Revolutionary 3D Printing Technique: Laser Sintering Unveiled
Title: Advancements in 3D Printing: Laser Sintering Revolutionizes Manufacturing IndustryIntroductionIn recent years, rapid technological advancements have transformed the way we manufacture products. One breakthrough in particular, 3D printing, has gained significant attention due to its potential to revolutionize various industries. One prominent technique within the realm of 3D printing is laser sintering, which has garnered praise for its ability to create highly intricate and functional objects. In this article, we explore the revolutionary impact of laser sintering in the manufacturing industry and examine its implementation at {}, a leading company at the forefront of this cutting-edge technology.Overview of Laser SinteringLaser sintering is a form of additive manufacturing that employs a high-powered laser to fuse powdered materials together, layer by layer, creating a solid three-dimensional object. Unlike traditional manufacturing techniques, which often involve removing or reshaping materials, laser sintering adds material only where it is needed, reducing waste and enabling the creation of complex geometries. This revolutionary method has opened up new possibilities across various industries and has significantly streamlined the production process.Application in ManufacturingWith its ability to produce highly intricate and functional objects, laser sintering has found numerous applications in the manufacturing industry. One key advantage of this technique is its versatility in handling a wide range of materials, including metals, polymers, ceramics, and composites. This flexibility has enabled manufacturers to explore novel designs and experiment with different materials, resulting in superior product performance.Another notable advantage of laser sintering is its potential for mass customization. This means that manufacturers can tailor each product to meet specific customer requirements, without compromising on cost or efficiency. This level of customization opens up new opportunities for personalized manufacturing, making it an attractive prospect for industries such as healthcare, aerospace, and automotive, where unique, patient-specific or niche products are increasingly in demand.Implementation at {}{}, a pioneering company in the field of laser sintering, has successfully harnessed the capabilities of this technology to deliver groundbreaking solutions across industries. Leveraging their expertise in 3D printing, the company has developed a range of advanced laser sintering machines that offer unparalleled precision and efficiency.The company's innovative equipment enables manufacturers to achieve high-resolution prints, ensuring accurate and consistent production. By utilizing powerful lasers and state-of-the-art software, their machines allow for intricate structures, superior surface finishes, and reduced post-processing requirements. This not only accelerates the production cycle but also cuts down on material waste, making laser sintering an eco-friendly option for forward-thinking companies.Moreover, {} has placed a strong emphasis on user-friendliness and accessibility. By incorporating intuitive interfaces and automated processes, their machinery has made laser sintering accessible even to those with limited technical expertise. This democratization of technology allows smaller businesses to adopt 3D printing for their manufacturing needs, leveling the playing field and fostering innovation across the industry.Future ImplicationsAs laser sintering continues to advance, the manufacturing landscape is poised for a significant transformation. The ability to create intricate and customized parts, reduce waste, and enhance the overall efficiency of production processes opens up new opportunities for businesses to thrive. With the growing adoption of laser sintering technology, industries such as healthcare, aerospace, automotive, and consumer goods are likely to witness an unprecedented era of manufacturing excellence.ConclusionLaser sintering, a groundbreaking technique within the realm of 3D printing, has revolutionized the manufacturing industry. By enabling highly intricate designs, mass customization, and reduction in waste, this technology offers immense potential for manufacturers across multiple sectors. With {} leading the charge in developing innovative laser sintering machines, the industry is set to experience a remarkable surge in productivity and efficiency. As we enter this new era of manufacturing, laser sintering is poised to redefine the boundaries of what is possible, paving the way for a more sustainable and customized future.
Discover the Latest Developments in Electronic Sheet Metal Parts
Title: Industry Innovator Launches Innovative Electronic Sheet Metal Parts for Enhanced Manufacturing EfficiencyIntroduction:[Company Name], a renowned leader in the manufacturing industry, is once again pushing the boundaries of innovation with its latest offering. With an unwavering commitment to providing cutting-edge solutions, [Company Name] has unveiled a revolutionary range of electronic sheet metal parts that promises to enhance manufacturing efficiency and revolutionize industrial operations.Paragraph 1:This new line of electronic sheet metal parts offered by [Company Name] is set to transform the manufacturing sector by fusing advanced technology with traditional sheet metal fabrication techniques. By leveraging their extensive industry experience, the company has successfully developed a range of parts that are optimized for seamless integration into a wide array of manufacturing processes. This innovation is poised to streamline production capabilities while significantly reducing costs and increasing overall efficiency.Paragraph 2:One of the key advantages of [Company Name]'s electronic sheet metal parts lies in the enhanced precision and consistency they bring to manufacturing processes. These parts are meticulously engineered using state-of-the-art tools and techniques, ensuring exacting adherence to design specifications. This level of precision translates into superior product quality and reduced defects, thereby positively impacting the overall manufacturing output.Paragraph 3:Moreover, the electronic sheet metal parts offered by [Company Name] are designed to cater to a diverse range of industrial applications. From the automotive and aerospace sectors to telecommunications and consumer electronics, these parts are engineered to meet the stringent requirements of various industries. Their versatility enables manufacturers from different sectors to effectively implement their design concepts and ideas in a streamlined and cost-effective manner.Paragraph 4:As a global manufacturing solutions provider, [Company Name] understands the importance of speed-to-market and offers quick turnaround times for its electronic sheet metal parts. By optimizing their production processes and utilizing the latest manufacturing technologies, the company is able to deliver these parts promptly, allowing manufacturers to maintain tight production schedules and respond rapidly to market demands.Paragraph 5:In addition to their cutting-edge design and precision manufacturing, [Company Name]'s electronic sheet metal parts are also built to withstand rigorous environmental conditions. They are crafted from high-quality materials that provide robustness and durability, ensuring their longevity even in challenging operational scenarios. This durability contributes to reduced maintenance costs and enhances the overall reliability of the final products.Paragraph 6:Customers of [Company Name] can also benefit from their commitment to exceptional customer service. The company's dedicated team assists clients through every step of the process, from initial product design to final production. This personalized approach ensures that manufacturing companies receive tailored solutions that align seamlessly with their specific needs, enabling them to optimize their operations and maximize their profitability.Conclusion:With the launch of their innovative electronic sheet metal parts, [Company Name] continues to revolutionize the manufacturing industry. Through their commitment to precision, versatility, durability, and unparalleled customer service, the company empowers manufacturers across various sectors to push the boundaries of engineering and manufacturing, paving the way for a more efficient and technologically advanced future.
Advanced 5 Axis CNC Milling: Everything You Need to Know
5 Axis CNC Milling Technology: Revolutionizing Manufacturing ProcessesThe manufacturing industry has witnessed an unprecedented revolution with the advancement of 5 Axis CNC milling technology. This cutting-edge technology has proven to significantly enhance efficiency, precision, and capability in the manufacturing processes, ultimately leading to higher productivity and superior quality products.{Company Name} is at the forefront of embracing this revolutionary technology and has successfully integrated 5 Axis CNC milling into its manufacturing operations. With over [X] years of experience in the industry, {Company Name} has established itself as a leading provider of high-quality manufacturing solutions. The adoption of 5 Axis CNC milling technology has further strengthened the company's position as an innovative and forward-thinking manufacturer.So, what exactly is 5 Axis CNC milling and how does it differ from traditional 3 Axis milling? In traditional 3 Axis milling, the cutting tool moves in three different axes to remove material from the workpiece. This process is limited in its ability to access certain angles and contours, leading to the need for multiple setups and adjustments to achieve the desired precision. On the other hand, 5 Axis CNC milling allows the cutting tool to move in five different axes, enabling it to approach the workpiece from any direction. This flexibility eliminates the need for multiple setups and adjustments, resulting in a more efficient and precise manufacturing process.The benefits of 5 Axis CNC milling technology are manifold. Firstly, it allows for the production of complex and intricate parts with unparalleled precision. The additional axes enable the cutting tool to reach angles and contours that were previously unattainable, resulting in the creation of highly detailed and accurate components. This level of precision is particularly crucial in industries such as aerospace, automotive, and medical, where the slightest deviation can have severe repercussions.Furthermore, 5 Axis CNC milling technology also significantly reduces production time and costs. With the ability to approach the workpiece from multiple angles in a single setup, the need for repositioning and readjusting the workpiece is eliminated. This not only saves time but also reduces the likelihood of human error, leading to a more streamlined and efficient manufacturing process. Additionally, the enhanced precision of 5 Axis CNC milling reduces material wastage, further contributing to cost savings for manufacturers.{Company Name} has leveraged the capabilities of 5 Axis CNC milling technology to offer a diverse range of manufacturing solutions to its clients. From prototyping and custom component manufacturing to large-scale production runs, the company has successfully catered to the needs of various industries with unparalleled precision and efficiency. The ability to manufacture complex and intricate parts with minimal setup and production time has allowed {Company Name} to stay ahead of the competition and provide its clients with superior products.The adoption of 5 Axis CNC milling technology has undoubtedly set {Company Name} apart as an industry leader in manufacturing. With a commitment to embracing innovation and leveraging cutting-edge technologies, the company continues to deliver exceptional results to its clients while pushing the boundaries of what is possible in the manufacturing industry.In conclusion, 5 Axis CNC milling technology has revolutionized the manufacturing processes, offering unparalleled precision, efficiency, and capability. {Company Name} stands as a shining example of a manufacturer that has successfully embraced this technology to offer superior manufacturing solutions to its clients. As the industry continues to evolve, it is evident that 5 Axis CNC milling will remain a driving force behind the advancement of manufacturing processes, shaping the future of the industry for years to come.
Sintering in 3D Printing: Exploring Advanced Manufacturing Techniques
Sintering Technology Advancements in 3D Printing: Revolutionizing Manufacturing ProcessesIn recent years, the field of 3D printing has experienced remarkable advancements, opening up new possibilities in various industries. One of the key breakthroughs is the development of sintering technology, which has revolutionized the manufacturing processes. This innovative technique allows for the creation of complex and durable objects by fusing together powders under high heat and pressure. Among the pioneers in this field is a company that has been at the forefront of 3D printing innovation, constantly pushing the boundaries of what is possible.Introduction to the CompanyEstablished in [year], {} has been a driving force in the 3D printing industry, consistently introducing cutting-edge technologies to the market. With a dedicated team of researchers and engineers, the company has become synonymous with innovation, constantly striving to enhance the capabilities of additive manufacturing. Through the utilization of sintering technology, they have been able to overcome previous limitations, opening up a whole new world of possibilities for the manufacturing sector.Sintering Process in 3D PrintingSintering is a process that involves compacting and forming solid objects from powders using heat and pressure. In the realm of 3D printing, sintering has proven to be a game-changer, allowing for the production of robust and intricate parts that were previously unachievable. While there are various sintering techniques, the one employed by {} is known as selective laser sintering (SLS).Selective Laser Sintering (SLS)With SLS, a laser selectively melts and fuses together successive layers of powdered material, precisely building the desired object layer-by-layer. This process is facilitated by a powder bed, which serves as the material reservoir. The advantage of SLS lies in its ability to work with a wide range of materials, including plastics, metals, ceramics, and even glass. This versatility has immense implications for applications across many industries, including aerospace, automotive, healthcare, and consumer goods.Advantages of Sintering TechnologySintering technology offers several advantages over traditional manufacturing processes, making it a preferred choice for many businesses. One significant advantage is the ability to create complex geometries that cannot be achieved using traditional methods. Through 3D printing and sintering, intricate designs with internal structures and cavities are made possible, reducing the need for assembly and enhancing overall product performance.Moreover, sintering technology allows for the production of parts with excellent mechanical properties. The fusion of powders under high heat and pressure yields objects that are incredibly durable, with high strength-to-weight ratios. This makes sintering ideal for applications that require lightweight yet robust components, such as aerospace and automotive industries.Furthermore, the flexibility of sintering allows for quick design iterations and customized manufacturing. As there is no need for molds or tooling, the production process can be more cost-effective and time-efficient. This flexibility also enables on-demand manufacturing, reducing inventory costs and wastage. The medical industry, for instance, has benefitted greatly from this capability, with personalized implants and prosthetics being produced more efficiently.Future Prospects and Economic ImpactsThe utilization of sintering technology in 3D printing has the potential to revolutionize the manufacturing industry. As this technique becomes more refined and accessible, it is expected to disrupt traditional production methods significantly. The decreased reliance on traditional manufacturing processes, such as machining and molding, will lead to cost reduction, increased efficiency, and improved sustainability.Additionally, with the growing demand for customization and personalized products, sintering technology offers manufacturers the opportunity to cater to individual needs on a larger scale. This shift towards mass customization is expected to reshape the manufacturing landscape, with 3D printing and sintering playing a pivotal role.ConclusionThe advancements in sintering technology within the realm of 3D printing have unlocked tremendous potential for various industries. With {} leading the way in innovative additive manufacturing, the possibilities seem endless. By harnessing the power of sintering, companies can now produce complex, durable, and customized objects, revolutionizing the way things are manufactured. As this technology continues to evolve, it is poised to reshape the manufacturing industry, opening up new horizons and driving economic growth.
Expert CNC Machine Services for Efficient Operations
CNC Machine Working Company, a renowned leader in the field of precision engineering and manufacturing, has been making waves in the industry with its innovative and efficient solutions. With a strong focus on cutting-edge technology and a commitment to delivering high-quality products, the company has established itself as a trusted partner for a wide range of clients across various sectors.The company prides itself on its state-of-the-art facilities, which are equipped with the latest CNC machines and advanced manufacturing tools. This allows them to handle projects of various scales and complexities, from small-scale prototypes to large-scale production runs. With a team of highly skilled and experienced engineers and technicians, they are able to provide custom machining solutions to meet the unique needs of each client.One of the key differentiators for CNC Machine Working Company is their dedication to quality and precision. Every product that comes out of their facilities undergoes rigorous quality control checks to ensure that it meets the highest standards. This commitment to excellence has earned them a reputation for reliability and consistency, making them the go-to partner for clients who demand nothing but the best.In addition to their cutting-edge technology and uncompromising quality standards, CNC Machine Working Company places a strong emphasis on customer satisfaction. They understand that every client has unique requirements and are committed to working closely with them to ensure that their needs are met. This customer-centric approach has resulted in long-term partnerships with many clients who value the company's reliability and professionalism.One of the key aspects of CNC Machine Working Company's success is their ability to adapt to the ever-changing needs of the industry. They continuously invest in new technologies and training for their staff to stay ahead of the curve and provide innovative solutions to their clients. This forward-thinking approach has enabled them to remain at the forefront of the industry and maintain their competitive edge.Recently, CNC Machine Working Company has introduced a new range of services aimed at expanding their capabilities and reaching new markets. The company has invested in advanced CNC machines that can handle a wider range of materials and deliver even more precise results. This has opened up new opportunities for them to work with clients from industries such as aerospace, automotive, and medical devices, where precision and quality are of the utmost importance.Furthermore, the company has also expanded its capacity to handle larger production volumes, allowing them to take on more ambitious projects and meet the growing demands of their clients. This development has positioned them as a one-stop solution provider for clients who require complex machining and manufacturing services on a large scale.In response to the growing demand for sustainable manufacturing solutions, CNC Machine Working Company has also made significant investments in environmentally friendly practices. They have implemented energy-efficient processes and reduced waste generation, demonstrating their commitment to sustainability and corporate responsibility.Looking ahead, CNC Machine Working Company is poised for continued growth and success in the industry. With their solid foundation of cutting-edge technology, unwavering commitment to quality, and customer-centric approach, they are well-positioned to meet the evolving needs of their clients and continue to be a leader in precision engineering and manufacturing.As CNC Machine Working Company continues to expand its capabilities and reach new heights, they are set to solidify their position as a trusted partner for clients who value excellence, innovation, and reliability in their manufacturing and engineering solutions.
Top Examples of Precision Machined Components for Various Industries
The machining industry is a crucial part of the manufacturing sector, as it provides essential components for a wide range of applications. Machined components are used in industries such as automotive, aerospace, medical devices, and consumer electronics, making them a vital part of our everyday lives. With advancements in technology and materials, the demand for high-quality machined components is ever-increasing.In this context, the company {} has been a leading supplier of precision machined components for over three decades. With state-of-the-art manufacturing facilities and a team of experienced engineers and technicians, the company has established itself as a reliable partner for businesses seeking top-notch machined components.One of the key strengths of {} is its ability to work with a variety of materials, including steel, aluminum, brass, and plastics. This versatility enables the company to cater to a diverse clientele with varying needs and requirements. Whether it's a large-scale production run or a one-off custom component, {} has the capabilities to deliver high-quality machined parts with precision and efficiency.Furthermore, the company's commitment to quality is evident in its adherence to strict quality control measures. Each machined component undergoes rigorous inspection and testing to ensure that it meets the highest standards of accuracy and performance. This dedication to quality has earned {} a stellar reputation in the industry, making it a preferred choice for many businesses across different sectors.To further enhance its capabilities, {} has invested in the latest CNC machining equipment and technology. This investment has enabled the company to produce complex and intricate machined components with speed and accuracy, meeting the evolving demands of the market. By staying at the forefront of technological advancements, {} remains well-positioned to cater to the ever-changing needs of its customers.In addition to its technical expertise, {} also takes pride in its customer-centric approach. The company works closely with clients to understand their specific requirements and provide tailored solutions that meet their needs. This collaborative and personalized approach has helped {} build long-lasting relationships with its customers, who rely on the company for their machined component needs.Looking ahead, {} is focused on continuous improvement and innovation. The company is exploring new materials and techniques to further expand its capabilities and offer cutting-edge solutions to its customers. By staying proactive and adaptable, {} aims to remain a top player in the machined component industry and continue serving its clients with excellence and reliability.In summary, machined components play a vital role in the manufacturing sector, and {} has emerged as a key player in this space. With its technical expertise, commitment to quality, and customer-centric approach, the company has established itself as a trusted supplier of precision machined components. As the demand for high-quality machined parts continues to grow, {} is well-equipped to meet these needs and contribute to the success of its clients across various industries.