Ultimate Guide to Vacuum Pressure Casting: Everything You Need to Know
By:Admin
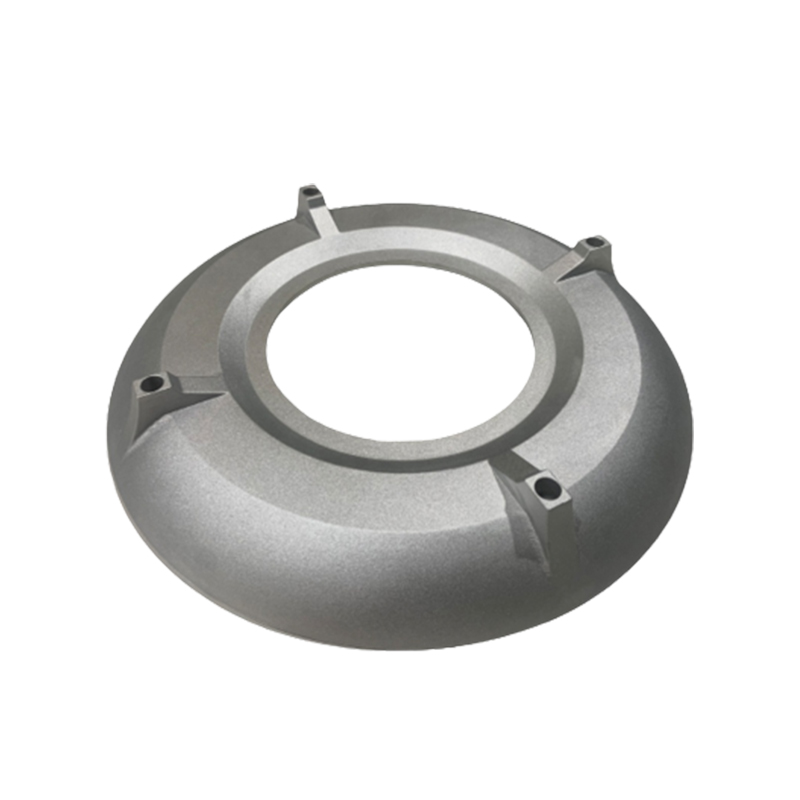
In the field of automotive manufacturing, vacuum pressure casting plays a crucial role in producing intricate and complex parts for vehicles. The process involves the creation of a mold in which molten metal is injected under vacuum and high pressure, resulting in superior casting quality and dimensional accuracy. This technique allows for the production of lightweight and durable automotive parts, contributing to the overall performance and efficiency of vehicles.
Moreover, vacuum pressure casting is also extensively used in the aerospace industry to produce components that meet the stringent requirements of the sector. By employing this advanced casting method, aerospace manufacturers can ensure the production of high-strength and precise parts that are crucial for the safety and reliability of aircraft and spacecraft.
Furthermore, the jewelry manufacturing industry also benefits from vacuum pressure casting as it allows for the creation of intricate and detailed jewelry pieces with exceptional precision. This sophisticated casting technique enables jewelry manufacturers to produce unique and delicate designs that meet the demands of discerning customers.
One company that has excelled in the field of vacuum pressure casting is {" company name"}. {"Company name"} is a leading provider of vacuum pressure casting solutions, offering a wide range of services to various industries around the world. With state-of-the-art facilities and cutting-edge technology, the company has earned a reputation for delivering high-quality and precision-cast components to its customers.
{"Company name"} has a team of highly skilled engineers and technicians who are dedicated to pushing the boundaries of vacuum pressure casting technology. They work closely with clients to understand their specific requirements and develop customized solutions that meet their needs and exceed their expectations.
{"Company name"}'s commitment to innovation and continuous improvement has allowed them to stay ahead of the competition and provide industry-leading vacuum pressure casting services. The company's dedication to quality and customer satisfaction has earned them a loyal client base and a strong reputation in the market.
In addition to vacuum pressure casting, {"company name"} also offers a wide range of other advanced manufacturing processes, including CNC machining, 3D printing, and rapid prototyping. This comprehensive suite of services enables the company to cater to a diverse range of industries and provide end-to-end manufacturing solutions to its clients.
With a strong focus on quality, precision, and innovation, {"company name"} continues to set new standards in the field of vacuum pressure casting. The company's commitment to excellence and its ability to deliver superior products have positioned it as a trusted partner for businesses across various industries.
In conclusion, vacuum pressure casting is a crucial manufacturing process that has revolutionized the production of high-quality and precise components in various industries. {"Company name"}'s expertise in this advanced casting technique, combined with its dedication to innovation and customer satisfaction, has established it as a leader in the field. As industries continue to demand superior casting solutions, {"company name"} is well-positioned to meet these needs and drive the evolution of vacuum pressure casting technology.
Company News & Blog
Precision Parts Processing: The Latest News
In the world of manufacturing, precision is key. This is especially true for the production of precision parts, which are crucial components in a wide range of industries, including aerospace, automotive, medical, and more. One company that has been making waves in the precision parts processing industry is {company name}. With their state-of-the-art CNC precision parts processing capabilities, {company name} has established itself as a leading provider of high-quality precision parts for a diverse range of applications.Founded in {year}, {company name} has quickly gained a reputation for excellence in the field of precision manufacturing. Specializing in CNC precision parts processing, the company has invested heavily in advanced equipment and technology to ensure that they can meet the exacting standards of their customers. Their commitment to quality and precision has made them a trusted partner for companies in a variety of industries, who rely on {company name} to deliver parts that meet their stringent specifications.One of the key differentiators for {company name} is their extensive experience and expertise in CNC precision parts processing. Their team of highly skilled engineers and technicians have the knowledge and capability to work with a wide range of materials, including aluminum, steel, titanium, and more. Whether it's a simple component or a complex, multi-part assembly, {company name} has the skills and technology to deliver precision parts that meet the highest standards.In addition to their technical expertise, {company name} also takes a customer-centric approach to their business. They understand that each customer has unique requirements and challenges, and they work closely with their clients to develop customized solutions that meet their specific needs. This commitment to customer satisfaction has earned {company name} a loyal and growing customer base, with clients who consistently rely on them for their precision parts processing needs.{company name} is also dedicated to staying at the forefront of technology and innovation in the precision parts processing industry. They regularly invest in new equipment and technologies to ensure that they can continue to meet the evolving needs of their customers. Their ongoing commitment to research and development has allowed them to stay ahead of the curve and offer cutting-edge solutions for even the most demanding applications.Looking to the future, {company name} is well-positioned to continue their success in the precision parts processing industry. With their strong focus on quality, precision, and customer satisfaction, they are poised to expand their reach and serve an even broader range of industries and applications. As the demand for high-quality precision parts continues to grow, {company name} is ready to meet the challenge and continue to be a leader in the industry.In conclusion, {company name} has established itself as a trusted provider of precision parts processing, with a strong track record of delivering high-quality, reliable parts for a diverse range of applications. With their advanced CNC processing capabilities, commitment to customer satisfaction, and dedication to innovation, {company name} is poised to continue their success and remain a top choice for companies in need of precision parts.
Top 5 Benefits of Vacuum Casting Silicone Mold for Your Manufacturing Needs
Vacuum Casting Silicone Mold - Revolutionizing the Manufacturing IndustryIn today's rapidly evolving manufacturing industry, companies are constantly seeking innovative solutions to streamline their production processes and stay ahead of the competition. This is where Vacuum Casting Silicone Mold technology is making a huge impact, providing manufacturers with a cost-effective and efficient method for producing high-quality prototypes and low-volume production parts.The process involves creating a silicone mold using a master model, made typically using 3D printing or CNC machining, and then injecting polyurethane resin into the mold under vacuum pressure. This results in the production of highly accurate and detailed parts that closely resemble the original master model, making it an ideal solution for creating prototypes, concept models, and end-use parts.One company at the forefront of this cutting-edge technology is {}. Specializing in rapid prototyping and low-volume manufacturing, {} offers a comprehensive range of services to meet the diverse needs of its clients. With a state-of-the-art facility equipped with advanced machinery and a team of experienced engineers, the company has built a solid reputation for delivering top-quality products in a timely and efficient manner.The Vacuum Casting Silicone Mold process offered by {} is a game-changer for businesses looking to bring their product ideas to life rapidly. One of the key benefits of this technology is its ability to produce parts with complex geometries and fine details, making it an ideal choice for a wide range of industries, including automotive, aerospace, consumer electronics, and medical devices. Moreover, the versatility of materials available for casting allows for the production of parts with varying mechanical properties, colors, and finishes, providing manufacturers with the flexibility they need to meet their specific requirements.With an unwavering commitment to customer satisfaction, {} takes a collaborative approach to every project, working closely with clients to understand their unique needs and provide customized solutions. From the initial design phase to the final production, the company's team of experts remains dedicated to ensuring the success of each and every project. This level of dedication has earned {} a loyal customer base and solidified its position as a leader in the industry.In addition to its technical expertise, {} places a strong emphasis on sustainability and environmental responsibility. The Vacuum Casting Silicone Mold process offered by the company is known for its minimal material wastage and energy efficiency, making it a greener alternative to traditional manufacturing methods. By embracing this eco-friendly approach, {} is not only contributing to a cleaner planet but also helping its clients reduce their carbon footprint and operate more responsibly.As the manufacturing industry continues to evolve, the demand for rapid prototyping and low-volume production solutions is only expected to grow. With its innovative Vacuum Casting Silicone Mold technology, combined with its unwavering commitment to quality and customer satisfaction, {} is well-positioned to meet this demand effectively.In conclusion, Vacuum Casting Silicone Mold technology is revolutionizing the manufacturing industry, providing companies with a cost-effective, efficient, and environmentally friendly solution for producing high-quality prototypes and low-volume production parts. With its advanced capabilities and customer-centric approach, {} is leading the way in delivering innovative manufacturing solutions, shaping the future of the industry.
Ultimate Guide to Vacuum Pressure Casting: Everything You Need to Know
Vacuum pressure casting is a manufacturing process that utilizes vacuum and pressure to produce high-quality and precise castings. This innovative technique is widely utilized in various industries, including automotive, aerospace, and jewelry manufacturing.In the field of automotive manufacturing, vacuum pressure casting plays a crucial role in producing intricate and complex parts for vehicles. The process involves the creation of a mold in which molten metal is injected under vacuum and high pressure, resulting in superior casting quality and dimensional accuracy. This technique allows for the production of lightweight and durable automotive parts, contributing to the overall performance and efficiency of vehicles.Moreover, vacuum pressure casting is also extensively used in the aerospace industry to produce components that meet the stringent requirements of the sector. By employing this advanced casting method, aerospace manufacturers can ensure the production of high-strength and precise parts that are crucial for the safety and reliability of aircraft and spacecraft.Furthermore, the jewelry manufacturing industry also benefits from vacuum pressure casting as it allows for the creation of intricate and detailed jewelry pieces with exceptional precision. This sophisticated casting technique enables jewelry manufacturers to produce unique and delicate designs that meet the demands of discerning customers.One company that has excelled in the field of vacuum pressure casting is {" company name"}. {"Company name"} is a leading provider of vacuum pressure casting solutions, offering a wide range of services to various industries around the world. With state-of-the-art facilities and cutting-edge technology, the company has earned a reputation for delivering high-quality and precision-cast components to its customers.{"Company name"} has a team of highly skilled engineers and technicians who are dedicated to pushing the boundaries of vacuum pressure casting technology. They work closely with clients to understand their specific requirements and develop customized solutions that meet their needs and exceed their expectations.{"Company name"}'s commitment to innovation and continuous improvement has allowed them to stay ahead of the competition and provide industry-leading vacuum pressure casting services. The company's dedication to quality and customer satisfaction has earned them a loyal client base and a strong reputation in the market.In addition to vacuum pressure casting, {"company name"} also offers a wide range of other advanced manufacturing processes, including CNC machining, 3D printing, and rapid prototyping. This comprehensive suite of services enables the company to cater to a diverse range of industries and provide end-to-end manufacturing solutions to its clients.With a strong focus on quality, precision, and innovation, {"company name"} continues to set new standards in the field of vacuum pressure casting. The company's commitment to excellence and its ability to deliver superior products have positioned it as a trusted partner for businesses across various industries.In conclusion, vacuum pressure casting is a crucial manufacturing process that has revolutionized the production of high-quality and precise components in various industries. {"Company name"}'s expertise in this advanced casting technique, combined with its dedication to innovation and customer satisfaction, has established it as a leader in the field. As industries continue to demand superior casting solutions, {"company name"} is well-positioned to meet these needs and drive the evolution of vacuum pressure casting technology.
Advanced 5 Axis CNC Milling: Everything You Need to Know
5 Axis CNC Milling Technology: Revolutionizing Manufacturing ProcessesThe manufacturing industry has witnessed an unprecedented revolution with the advancement of 5 Axis CNC milling technology. This cutting-edge technology has proven to significantly enhance efficiency, precision, and capability in the manufacturing processes, ultimately leading to higher productivity and superior quality products.{Company Name} is at the forefront of embracing this revolutionary technology and has successfully integrated 5 Axis CNC milling into its manufacturing operations. With over [X] years of experience in the industry, {Company Name} has established itself as a leading provider of high-quality manufacturing solutions. The adoption of 5 Axis CNC milling technology has further strengthened the company's position as an innovative and forward-thinking manufacturer.So, what exactly is 5 Axis CNC milling and how does it differ from traditional 3 Axis milling? In traditional 3 Axis milling, the cutting tool moves in three different axes to remove material from the workpiece. This process is limited in its ability to access certain angles and contours, leading to the need for multiple setups and adjustments to achieve the desired precision. On the other hand, 5 Axis CNC milling allows the cutting tool to move in five different axes, enabling it to approach the workpiece from any direction. This flexibility eliminates the need for multiple setups and adjustments, resulting in a more efficient and precise manufacturing process.The benefits of 5 Axis CNC milling technology are manifold. Firstly, it allows for the production of complex and intricate parts with unparalleled precision. The additional axes enable the cutting tool to reach angles and contours that were previously unattainable, resulting in the creation of highly detailed and accurate components. This level of precision is particularly crucial in industries such as aerospace, automotive, and medical, where the slightest deviation can have severe repercussions.Furthermore, 5 Axis CNC milling technology also significantly reduces production time and costs. With the ability to approach the workpiece from multiple angles in a single setup, the need for repositioning and readjusting the workpiece is eliminated. This not only saves time but also reduces the likelihood of human error, leading to a more streamlined and efficient manufacturing process. Additionally, the enhanced precision of 5 Axis CNC milling reduces material wastage, further contributing to cost savings for manufacturers.{Company Name} has leveraged the capabilities of 5 Axis CNC milling technology to offer a diverse range of manufacturing solutions to its clients. From prototyping and custom component manufacturing to large-scale production runs, the company has successfully catered to the needs of various industries with unparalleled precision and efficiency. The ability to manufacture complex and intricate parts with minimal setup and production time has allowed {Company Name} to stay ahead of the competition and provide its clients with superior products.The adoption of 5 Axis CNC milling technology has undoubtedly set {Company Name} apart as an industry leader in manufacturing. With a commitment to embracing innovation and leveraging cutting-edge technologies, the company continues to deliver exceptional results to its clients while pushing the boundaries of what is possible in the manufacturing industry.In conclusion, 5 Axis CNC milling technology has revolutionized the manufacturing processes, offering unparalleled precision, efficiency, and capability. {Company Name} stands as a shining example of a manufacturer that has successfully embraced this technology to offer superior manufacturing solutions to its clients. As the industry continues to evolve, it is evident that 5 Axis CNC milling will remain a driving force behind the advancement of manufacturing processes, shaping the future of the industry for years to come.
Revolutionary 3D Printing Technique: Laser Sintering Unveiled
Title: Advancements in 3D Printing: Laser Sintering Revolutionizes Manufacturing IndustryIntroductionIn recent years, rapid technological advancements have transformed the way we manufacture products. One breakthrough in particular, 3D printing, has gained significant attention due to its potential to revolutionize various industries. One prominent technique within the realm of 3D printing is laser sintering, which has garnered praise for its ability to create highly intricate and functional objects. In this article, we explore the revolutionary impact of laser sintering in the manufacturing industry and examine its implementation at {}, a leading company at the forefront of this cutting-edge technology.Overview of Laser SinteringLaser sintering is a form of additive manufacturing that employs a high-powered laser to fuse powdered materials together, layer by layer, creating a solid three-dimensional object. Unlike traditional manufacturing techniques, which often involve removing or reshaping materials, laser sintering adds material only where it is needed, reducing waste and enabling the creation of complex geometries. This revolutionary method has opened up new possibilities across various industries and has significantly streamlined the production process.Application in ManufacturingWith its ability to produce highly intricate and functional objects, laser sintering has found numerous applications in the manufacturing industry. One key advantage of this technique is its versatility in handling a wide range of materials, including metals, polymers, ceramics, and composites. This flexibility has enabled manufacturers to explore novel designs and experiment with different materials, resulting in superior product performance.Another notable advantage of laser sintering is its potential for mass customization. This means that manufacturers can tailor each product to meet specific customer requirements, without compromising on cost or efficiency. This level of customization opens up new opportunities for personalized manufacturing, making it an attractive prospect for industries such as healthcare, aerospace, and automotive, where unique, patient-specific or niche products are increasingly in demand.Implementation at {}{}, a pioneering company in the field of laser sintering, has successfully harnessed the capabilities of this technology to deliver groundbreaking solutions across industries. Leveraging their expertise in 3D printing, the company has developed a range of advanced laser sintering machines that offer unparalleled precision and efficiency.The company's innovative equipment enables manufacturers to achieve high-resolution prints, ensuring accurate and consistent production. By utilizing powerful lasers and state-of-the-art software, their machines allow for intricate structures, superior surface finishes, and reduced post-processing requirements. This not only accelerates the production cycle but also cuts down on material waste, making laser sintering an eco-friendly option for forward-thinking companies.Moreover, {} has placed a strong emphasis on user-friendliness and accessibility. By incorporating intuitive interfaces and automated processes, their machinery has made laser sintering accessible even to those with limited technical expertise. This democratization of technology allows smaller businesses to adopt 3D printing for their manufacturing needs, leveling the playing field and fostering innovation across the industry.Future ImplicationsAs laser sintering continues to advance, the manufacturing landscape is poised for a significant transformation. The ability to create intricate and customized parts, reduce waste, and enhance the overall efficiency of production processes opens up new opportunities for businesses to thrive. With the growing adoption of laser sintering technology, industries such as healthcare, aerospace, automotive, and consumer goods are likely to witness an unprecedented era of manufacturing excellence.ConclusionLaser sintering, a groundbreaking technique within the realm of 3D printing, has revolutionized the manufacturing industry. By enabling highly intricate designs, mass customization, and reduction in waste, this technology offers immense potential for manufacturers across multiple sectors. With {} leading the charge in developing innovative laser sintering machines, the industry is set to experience a remarkable surge in productivity and efficiency. As we enter this new era of manufacturing, laser sintering is poised to redefine the boundaries of what is possible, paving the way for a more sustainable and customized future.
Expert Guide: Mastering the Art of CNC Machine Work for Enhanced Precision and Efficiency!
Title: Revolutionizing Manufacturing: The Next Generation of CNC Machine WorkIntroduction:The manufacturing industry has come a long way in embracing technological advancements to streamline operations and enhance efficiency. Among the latest breakthroughs is the implementation of Computer Numerical Control (CNC) machines, which have revolutionized precision engineering and machining processes. This news article explores the cutting-edge developments in CNC machine work, highlighting its potential to transform diverse industries.1. Increasing Precision and Accuracy:CNC machines have proven to be game-changers for manufacturers seeking high precision and accuracy. By eliminating human errors and inconsistencies, these machines ensure uniformity in the manufacturing process, resulting in superior end products. The integration of advanced computer software enables CNC machines to precisely control cutting tools, creating intricate designs and complex shapes. This level of precision has opened new doors for industries such as aerospace, automotive, and medical, where strict tolerance and quality standards are paramount.2. Streamlined Workflow and Cost Efficiency:The automation capabilities of CNC machines significantly streamline workflow processes, reducing production time and costs. Offering seamless integration with Computer-Aided Design (CAD) software, manufacturers can easily translate digital designs into physical products. This eliminates the need for manual intervention at every step, minimizing errors and reducing labor costs. By optimizing material utilization and minimizing wastage, CNC machines also contribute to cost-effective manufacturing, making them indispensable assets for companies striving for profitability in today's competitive market.3. Enhanced Safety and Employee Well-being:Prioritizing employee well-being and safety is a cornerstone of any successful manufacturing business. CNC machines contribute to achieving this goal by minimizing the risk of workplace accidents and injuries. With automated controls, workers can manage the machining process remotely, reducing their exposure to hazardous environments. The utilization of CNC machines ensures operators are shielded from potentially harmful processes, such as metal cutting or molding, enhancing overall workplace safety.4. Versatility and Adaptability:CNC machines have advanced the concept of versatility in manufacturing. They are capable of performing a wide range of operations, including milling, turning, drilling, and grinding. These machines can seamlessly switch between tasks, enabling manufacturers to produce a diverse array of components with ease. Whether it is mass-producing identical parts or creating intricate custom designs, CNC machines offer unparalleled flexibility, adaptability, and speed, providing manufacturers with a competitive edge.5. 24/7 Production Capability:The relentless pursuit of increased productivity and reduced downtime has led to the development of CNC machines designed for continuous operation. By enabling 24/7 production capabilities, manufacturers can optimize their output and meet demanding customer requirements. CNC machines excel at maintaining consistent performance over extended periods, ensuring product quality remains uncompromised. This capability proves vital in time-sensitive industries that require rapid response times and uninterrupted production.6. Impact on Employment Opportunities:Although automation and technological advancements may raise concerns about job losses, the implementation of CNC machines has, in fact, created new employment opportunities. While some manual jobs have become obsolete, the demand for skilled technicians and programmers to operate and maintain CNC machines has risen. Manufacturers are investing in training programs to bridge the skills gap, allowing workers to adapt to the changing landscape. This emphasis on upskilling ensures sustainable employment for the workforce while harnessing the benefits of CNC machine work.Conclusion:As the manufacturing industry continues to embrace digital transformation, CNC machine work has emerged as a powerful tool to propel innovation and growth. With its precision, automation, adaptability, and cost efficiency, the potential applications of CNC machines span across various sectors. The integration of CNC machine work into manufacturing processes enables companies to optimize output, improve product quality, and stay ahead of their competition. Embracing this cutting-edge technology sets the stage for a future where efficiency and customer satisfaction go hand in hand.
Find Local CNC Milling Companies for Your Machining Needs
The demand for CNC milling services has been on the rise, and many businesses are looking for reliable and efficient CNC milling companies located near them. One such company that has been gaining attention in the industry is {}. With their state-of-the-art manufacturing facility and team of experienced professionals, they have become a preferred choice for businesses looking for precision CNC milling services.{} is a leading CNC milling company that specializes in providing high-quality machining and prototyping services to a wide range of industries. Their facility is equipped with the latest CNC milling machines and technology, allowing them to produce complex and intricate parts with tight tolerances. The company has earned a reputation for delivering reliable and cost-effective solutions to their customers, making them a trusted partner for many businesses in need of CNC milling services.In addition to their cutting-edge technology, {} takes pride in their team of skilled machinists and engineers who are dedicated to providing top-notch services. They work closely with their clients to understand their specific requirements and ensure that they deliver products that meet or exceed their expectations. The company’s commitment to quality and customer satisfaction has earned them a loyal customer base and positioned them as a leading CNC milling company in the industry.One of the key advantages of choosing {} for CNC milling services is their ability to handle a wide range of materials. Whether it’s aluminum, steel, titanium, or plastics, their team has the expertise and capabilities to work with various materials and deliver superior results. This versatility has made them a go-to choice for businesses in industries such as aerospace, automotive, medical, and more.Moreover, {} understands the importance of quick turnaround times in the manufacturing industry. They have streamlined their processes to ensure efficient production and delivery of parts, allowing their clients to meet tight project deadlines and stay ahead of the competition. Their dedication to on-time delivery and reliability has set them apart from other CNC milling companies in the area.As a customer-focused company, {} also places a strong emphasis on communication and transparency throughout the CNC milling process. They keep their clients informed at every stage of the production, from initial design to final inspection, to ensure that the end product meets the required specifications. This open and collaborative approach has helped them build strong, long-lasting relationships with their clients, who continue to rely on {} for their CNC milling needs.In conclusion, the demand for reliable CNC milling companies near me continues to grow, and {} has emerged as a top choice for businesses in need of precision machining services. With their advanced technology, skilled team, and commitment to quality, they have positioned themselves as a leading CNC milling company in the industry. Whether it’s prototyping, production runs, or custom projects, {} has the expertise and capabilities to deliver exceptional results. Businesses looking for a trusted partner for their CNC milling needs can rely on {} to provide cost-effective solutions and superior service.
Transform Your Designs with Vacuum Casting 3D Printing Technologies
Vacuum Casting 3D Printing revolutionizes the Manufacturing Industry[Date], [City] - The manufacturing industry has taken a giant leap forward with the introduction of Vacuum Casting 3D Printing technology. This revolutionary process, which combines the precision of 3D printing with the efficiency of vacuum casting, has opened up a whole new realm of possibilities for product development and production.[Company Name], a leader in advanced manufacturing solutions, has been at the forefront of this technology, reshaping the manufacturing landscape. With their innovative processes and cutting-edge equipment, they have successfully helped numerous companies overcome traditional manufacturing limitations, providing cost-effective and time-efficient solutions.Traditional manufacturing methods often come with significant limitations, including high production costs, long lead times, and limited design flexibility. However, Vacuum Casting 3D Printing offers a game-changing alternative. By utilizing a combination of 3D printing and vacuum casting, [Company Name] has been able to overcome these constraints, providing businesses with a streamlined manufacturing process.One of the key advantages of Vacuum Casting 3D Printing is its ability to produce highly complex and intricate designs that were previously difficult or impossible to achieve using conventional manufacturing methods. The process starts by creating a 3D printed mold, which is then used to produce a silicone mold through vacuum casting. This mold can then be used to create multiple copies of the original design, even with undercuts, intricate details, and delicate features. This provides manufacturers with the freedom to create complex parts that meet the strictest of demands.Another major benefit of Vacuum Casting 3D Printing is its cost-effectiveness, especially when compared to traditional manufacturing methods. The process eliminates the need for expensive tooling, molds, and machining setups, reducing overall production costs significantly. This not only makes it an attractive option for small and medium-sized enterprises but also enables larger companies to optimize their production processes by reducing costs and increasing efficiency.Speed is another remarkable advantage of Vacuum Casting 3D Printing. With traditional manufacturing, developing and producing a new product can take weeks or even months. However, the Vacuum Casting 3D Printing process drastically reduces lead times, enabling rapid prototyping and iterative design improvements. This allows companies to bring products to market faster, giving them a competitive edge in today's fast-paced business environment.[Company Name] has spearheaded the adoption of Vacuum Casting 3D Printing across various industries, including automotive, aerospace, consumer electronics, and medical devices. Their team of experts works closely with clients to understand their specific manufacturing needs, and they provide tailor-made solutions to optimize the production process. By combining their expertise in materials selection, 3D printing, and vacuum casting, [Company Name] ensures that clients receive the highest quality products with exceptional speed and accuracy."Our Vacuum Casting 3D Printing technology has revolutionized the way companies manufacture products," said [Company Spokesperson]. "We are proud to be helping businesses break free from the limitations of traditional manufacturing and embrace a more agile and efficient approach. With our expertise and state-of-the-art equipment, we are committed to driving innovation and delivering results that exceed our clients' expectations."The introduction of Vacuum Casting 3D Printing technology by [Company Name] has created ripples in the manufacturing industry. By addressing the limitations of traditional manufacturing methods, this innovative process offers a cost-effective and time-efficient alternative that unlocks new possibilities for product development and production. With such advancements, manufacturers can now bring their ideas to life more easily and faster than ever before, ushering in a new era of manufacturing excellence.
Quality CNC Milling Auto Parts for Efficient Manufacturing
Auto Parts Manufacturer Utilizes CNC Milling Technology to Enhance Product QualityIn the competitive world of auto parts manufacturing, precision and quality are key factors that determine the success of a company. One auto parts manufacturer, located in the heart of the industrial district, has been making significant strides in enhancing their product quality by utilizing advanced CNC milling technology.With over 20 years of experience in the industry, the company has established itself as a leading provider of high-quality auto parts for a wide range of vehicles. Specializing in the production of a variety of auto parts, including engine components, transmission parts, and suspension systems, the company has built a strong reputation for delivering reliable and durable products to its customers.In order to stay ahead of the competition and meet the increasing demands for precision and accuracy in auto parts manufacturing, the company made the strategic decision to invest in state-of-the-art CNC milling technology. CNC milling, short for computer numerical control milling, is a machining process that utilizes computerized controls and cutting tools to remove material from a workpiece and produce custom-designed parts with high precision.By leveraging CNC milling technology, the company is able to achieve a level of precision and consistency that was previously unattainable with traditional machining methods. This has resulted in a significant improvement in the quality and performance of their auto parts, ultimately enhancing the overall value proposition for their customers.One of the key advantages of CNC milling is its ability to produce complex and intricate shapes with unparalleled accuracy. With the ability to program the milling machine to follow precise instructions, the company is able to create intricate designs and tight tolerances that are essential for the functionality of auto parts.Furthermore, CNC milling technology allows for a high level of repeatability, ensuring that each part produced is identical to the next. This level of precision and consistency is crucial for maintaining the quality and reliability of the auto parts, ultimately contributing to the safety and performance of the end products.In addition to the technical advantages, CNC milling also offers increased efficiency and productivity. With the ability to automate the machining process and run multiple operations simultaneously, the company is able to reduce lead times and increase their production capacity to meet the growing demand for their products.Despite the initial investment in CNC milling technology, the company has found that the long-term benefits far outweigh the costs. By improving the quality and precision of their products, they have been able to attract new customers and expand their market share in the auto parts industry.Looking to the future, the company is committed to further leveraging advanced technologies to continuously improve their manufacturing processes and product offerings. With a dedicated team of engineers and machinists, they are constantly seeking new opportunities to enhance their capabilities and stay ahead of industry trends.As the demand for high-quality auto parts continues to grow, the company remains confident in their ability to meet the needs of their customers and deliver superior products that exceed expectations. By embracing CNC milling technology and a commitment to excellence, they are poised to maintain their position as a leading provider of auto parts for years to come.
Top 5 Types of Mould You Need to Know
Type Mould is a leading manufacturer of high-quality moulds for various industries, including automotive, packaging, and consumer goods. With a focus on innovation and precision engineering, Type Mould has established itself as a trusted supplier to numerous global brands.The company's commitment to excellence is reflected in its advanced manufacturing facilities and state-of-the-art technology. Type Mould's team of experienced engineers and technicians work tirelessly to develop moulds that meet the specific needs of their clients, ensuring the highest levels of quality and performance.In recent news, Type Mould has announced the launch of a new line of moulds that are designed to revolutionize the automotive industry. These innovative moulds are engineered to enhance the production process of automotive components, delivering greater efficiency and cost savings for manufacturers."We are excited to introduce our latest line of moulds that are specifically tailored to the automotive sector," said [Company Spokesperson]. "These moulds incorporate cutting-edge technology and design principles to address the evolving needs of the automotive industry, providing our clients with a competitive edge in the market."Type Mould's new automotive moulds are crafted with a focus on precision and durability. They are capable of producing complex and intricate automotive components with unparalleled accuracy, resulting in a significant reduction in production time and costs for manufacturers.Furthermore, these moulds are designed to withstand the high pressures and temperatures involved in automotive manufacturing processes, ensuring consistent and reliable performance over extended production runs. This durability ultimately translates to long-term savings for manufacturers, as the need for frequent maintenance and replacement of moulds is minimized.In addition to their technical capabilities, Type Mould's automotive moulds are also engineered with versatility in mind. They are adaptable to various manufacturing processes and can accommodate a wide range of materials, making them suitable for diverse automotive applications.The launch of this new line of automotive moulds solidifies Type Mould's position as an industry leader in the mould manufacturing sector. The company's dedication to continuous innovation and superior quality has earned them a stellar reputation among their clients, who rely on Type Mould for their moulding needs.With a strong track record of delivering innovative solutions to meet the demands of various industries, Type Mould continues to set benchmarks for excellence and reliability in the mould manufacturing sector. Their commitment to pushing the boundaries of technology and engineering ensures that they remain at the forefront of the industry, offering their clients the most advanced and efficient moulding solutions available.As the automotive industry continues to evolve and demand for high-quality components grows, Type Mould's new line of automotive moulds is poised to make a significant impact. Manufacturers can now leverage these advanced moulds to enhance their production processes, improve product quality, and ultimately, gain a competitive advantage in the market.With a strong foundation built on expertise, innovation, and customer satisfaction, Type Mould is well-positioned to continue leading the way in the mould manufacturing industry. Their relentless pursuit of excellence and commitment to delivering superior products underscores their status as a trusted partner for manufacturers across various sectors.