Revolutionizing 3D Printing: A Closer Look at SLS Technology
By:Admin
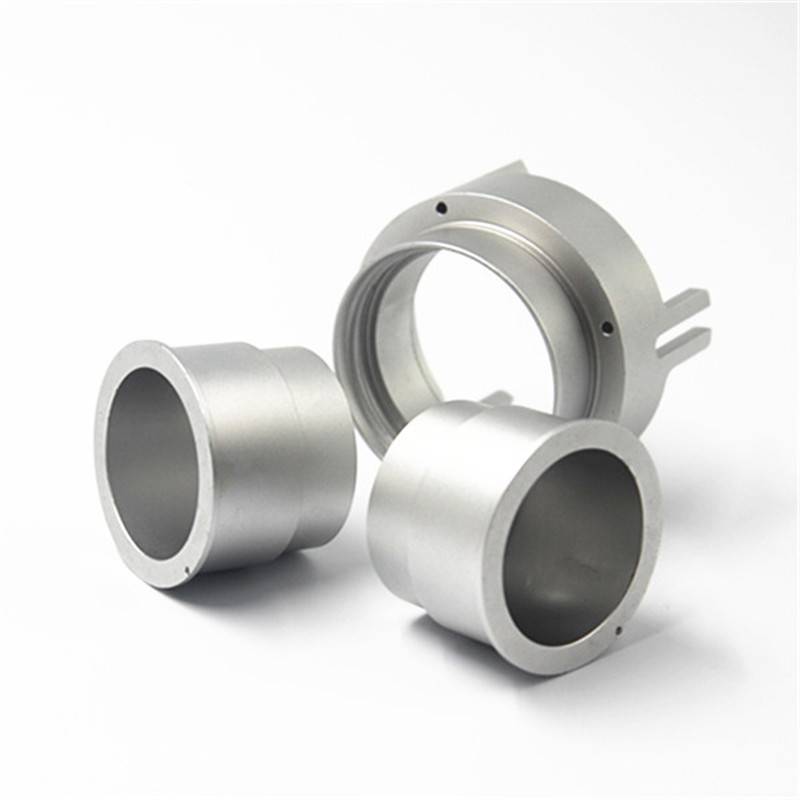
[News Introduction]:
In today's constantly evolving technological landscape, traditional manufacturing practices are being challenged by innovative and groundbreaking solutions. The advent of additive manufacturing, popularly known as 3D printing, has disrupted the industry by offering unparalleled efficiency, cost-effectiveness, and design possibilities. One of the frontrunners in this field, an emerging leader, is significantly transforming the way we think about manufacturing. Their innovative SLS printing technology has already begun revolutionizing various sectors by addressing key challenges and offering outstanding solutions.
[Company Introduction]:
The pioneering company, leveraging state-of-the-art manufacturing techniques and an impeccable understanding of industry needs, has emerged as an industry trailblazer. Founded on the principles of innovation, sustainability, and affordability, this cutting-edge organization has a track record of consistently pushing the boundaries of what is possible. Their SLS printing technology has gained widespread acclaim and recognition for its ability to transform complex designs into physical objects with stunning accuracy.
[Background]:
Traditional manufacturing processes often encounter limitations when it comes to creating intricate or customized designs. Conventional methods, such as injection molding or subtractive manufacturing, are time-consuming and costly. Prototyping and production can be resource-intensive, and the limitations tied to these techniques often hamper innovation and creativity. However, with the introduction of SLS printing, the game is set to change.
[SLS Printing Revolutionizing Manufacturing]:
SLS printing, short for Selective Laser Sintering, boasts several advantages over traditional manufacturing processes. Using powdered materials, such as plastics, metals, or ceramics, SLS printing creates three-dimensional objects by selectively fusing the powdered particles layer by layer. This process not only eliminates the need for expensive tooling but also unlocks endless possibilities for design complexity and customization.
Furthermore, SLS printing enables the creation of structures with intricate internal geometries, making it ideal for producing lightweight components that would be impossible through traditional means. The technology's ability to print objects with moving parts or integrated functionalities amplifies its potential applications across various industries.
In addition to its design flexibility, SLS printing also reduces waste compared to conventional manufacturing methods. By using only the necessary amount of raw material, it minimizes the ecological impact and material waste. Consequently, this groundbreaking technology aligns perfectly with the global shift towards sustainability and eco-friendly practices.
[Applications and Impact]:
The advent of SLS printing technology opens up exciting opportunities across multiple sectors. In the healthcare industry, medical professionals now have the ability to create custom implants tailored to individual patients, enhancing treatment outcomes and patient satisfaction. The aerospace industry benefits from lightweight yet structurally sound components, improving fuel efficiency and reducing emissions. Automotive manufacturers can now produce complex designs for customized parts and rapid prototyping, reducing production time and costs significantly.
Moreover, SLS printing empowers creative designers and artists by translating their intricate visions into physical reality. Artists can now produce sculptures and intricate artworks that were once deemed impossible to fabricate. Architects can design and print detailed scale models, enabling better visualization and collaboration with clients.
[Conclusion]:
As the manufacturing industry embraces the innovation and potential of SLS printing, the possibilities for growth and development are immense. This revolutionary technology not only enhances design flexibility and efficiency but also contributes to creating a more sustainable and environmentally conscious future. With its continuous efforts in pushing the boundaries of what is possible, the company has established itself as a key player driving the 3D printing revolution. As industries across the globe adopt SLS printing, it can be anticipated that we are witnessing the dawn of a new era in manufacturing.
Company News & Blog
Top Plastic Injection Manufacturers Providing High-Quality Products and Services
Title: Leading Plastic Injection Company Revolutionizes Manufacturing ProcessesIntroduction:In the ever-evolving world of manufacturing, innovative techniques and advanced technologies are crucial for staying ahead of the competition. One company that has successfully embraced these principles is a prominent plastic injection company. By establishing themselves as pioneers in the industry, they have revolutionized manufacturing processes, resulting in exceptional quality products and streamlined production timelines.Company Overview:The plastic injection company, (remove brand name), was founded in (year) with the vision of delivering cutting-edge solutions to industries ranging from automotive to consumer electronics. With an unwavering commitment to technological advancements, the company has consistently pushed the boundaries of what is possible in plastic injection molding. Through a customer-centric approach and a focus on sustainable practices, (remove brand name) has become a trusted partner for numerous renowned brands across the globe.Technological Advancements:In their quest for excellence, (remove brand name) has consistently invested in state-of-the-art machinery and innovative technologies. The company utilizes sophisticated computer-aided design (CAD) and computer-aided manufacturing (CAM) software to design and simulate the molds with utmost precision. This allows them to identify potential design flaws and make necessary adjustments early in the process, thereby reducing production costs and time.Furthermore, (remove brand name) has embraced automation to enhance efficiency and productivity. They have integrated robotics into their production lines to optimize repetitive tasks, ensuring consistent quality and minimizing human error. These cutting-edge technologies not only streamline the manufacturing process but also enhance the overall accuracy and repeatability of their products.Quality Control Measures:As a renowned plastic injection company, (remove brand name) places tremendous emphasis on maintaining the highest standards of quality throughout their manufacturing process. They employ a rigorous quality control program, starting from sourcing raw materials to the final inspection of finished products. By adhering to international quality certifications and utilizing advanced inspection equipment, (remove brand name) ensures that each product leaving their facility meets or exceeds customer expectations.Sustainable Practices:Recognizing their responsibility towards the environment, (remove brand name) has implemented various sustainable practices in their manufacturing processes. They adhere to strict recycling practices and promote the use of eco-friendly materials whenever possible. Through reducing waste generation and optimizing energy consumption, (remove brand name) minimizes their carbon footprint, contributing to a greener and cleaner planet.Collaborative Partnerships:A key factor behind the success of (remove brand name) is their collaborative approach with clients. By understanding the unique requirements and challenges of each customer, the company provides customized solutions that address their specific needs. From product design consultation to providing prototyping services, (remove brand name) actively collaborates with their clients, ensuring mutual success and establishing long-lasting partnerships.Plans for Future Growth:Looking towards the future, (remove brand name) aims to further advance their technological capabilities and expand their market reach. They plan to invest in research and development to drive innovation and continue delivering cutting-edge solutions to global industries. Additionally, (remove brand name) envisions strengthening their foothold in emerging markets, establishing themselves as a global leader in the plastic injection industry.Conclusion:Through their unwavering commitment to technological advancements, a customer-centric approach, and sustainable practices, (remove brand name) has revolutionized manufacturing processes. By consistently delivering high-quality products and optimizing production timelines, they have earned the trust and recognition of various industries worldwide. With their focus on future growth and innovation, (remove brand name) is set to redefine the plastic injection landscape and shape the future of manufacturing.
Enhancing Efficiency and Precision: The Advantages of Casting Injection Molding
Title: Advancements in Casting Injection Molding Revolutionize Manufacturing ProcessesIntroduction:Casting Injection Molding, developed by an industry-leading company, has emerged as a game-changing technology in the field of manufacturing processes. This cutting-edge technique combines the precision and flexibility of injection molding with the advantages of casting, leading to improved product quality, reduced costs, and increased production efficiency. This article explores the innovative potential of Casting Injection Molding and its implications for various industries.I. Understanding Casting Injection MoldingCasting Injection Molding is a technology that merges injection molding and casting, enabling manufacturers to produce complex parts with superior precision and reduced production time. By utilizing thermoplastics instead of traditional liquid metals, the process offers greater design flexibility while delivering high-quality components. The integration of innovative design software and advanced machinery allows for detailed 3D modeling and real-time feedback, ensuring optimal results.II. Enhanced Product QualityCasting Injection Molding removes many of the limitations associated with traditional casting techniques. The process utilizes a molten polymer that fills a mold cavity under high pressure, eradicating potential defects such as porosity, air bubbles, and shrinkage that are common with traditional casting. The homogeneous and isotropic characteristics of the material produce parts with consistent mechanical properties, resulting in higher product integrity and reliability. With improved repeatability, the technology enables manufacturers to achieve strict quality control standards, reduce waste, and deliver superior end products to consumers.III. Cost Reduction and Time EfficiencyThe use of Casting Injection Molding enhances cost efficiency throughout the manufacturing process. By allowing for faster cycle times, reduced labor requirements, and simplified tooling, companies can significantly lower production costs while maintaining consistent quality levels. Employing thermoplastics eliminates the need for expensive molds associated with traditional casting, reducing initial investment and enabling greater flexibility during the prototyping and testing stages. Additionally, the ability to produce complex parts in a single step eliminates secondary processes, streamlining production and minimizing time to market.IV. Application in Various IndustriesCasting Injection Molding has found applications across multiple industries, revolutionizing the manufacturing processes in diverse sectors. In the automotive industry, this technology has enabled the production of lightweight components with enhanced strength, contributing to fuel efficiency and reduced emissions. The healthcare sector has embraced Casting Injection Molding for precise and custom medical device manufacturing, facilitating improved patient care and better treatment outcomes. The aerospace industry has also witnessed advancements through this technique, with the production of complex components that meet stringent aviation standards while reducing weight and maintaining durability.V. Future Prospects and ImpactAs Casting Injection Molding continues to evolve, its impact on manufacturing processes is set to grow exponentially. The integration of artificial intelligence algorithms and machine learning capabilities will enhance process automation, enabling real-time adjustments and intelligent decision-making. The potential for utilizing sustainable materials, such as biodegradable thermoplastics or recycled polymers, opens up eco-friendly manufacturing opportunities. Furthermore, the ongoing exploration of new applications and industries promises to unlock additional benefits and further transform the manufacturing landscape.Conclusion:Casting Injection Molding, developed by {}, has emerged as a groundbreaking technology in the manufacturing industry. With its ability to produce high-quality components, reduce production costs, and enhance time efficiency, this innovative technique has already made a significant impact across various sectors. As the manufacturing landscape continues to evolve, Casting Injection Molding is positioned to revolutionize production processes, driving progress in sectors ranging from automotive and healthcare to aerospace and beyond.
CNC Lathe Machining: The Ultimate Guide for Precision Turning
CNC Lathe Machining Revolutionizes Manufacturing IndustryIn a world driven by technological advancements, precision and efficiency have become the cornerstone of manufacturing processes. One such significant innovation that has transformed the industry in recent years is CNC lathe machining. Removing the brand name, we take a closer look at this groundbreaking technology that has revolutionized the manufacturing sector.CNC lathe machining, also known as computer numerical control lathe machining, is a manufacturing process that utilizes computerized controls and automated systems to produce intricate and precise parts. This highly advanced technique has completely transformed traditional turning processes, offering a range of benefits that have propelled companies to adopt this technology.One key advantage of CNC lathe machining is its unparalleled precision. The computerized controls ensure that every component is produced with utmost accuracy, eliminating human errors that may arise in traditional manual operations. This precise machining capability enables manufacturers to produce complex designs and intricate parts that were once impracticable with traditional methods.Speed and efficiency are also significant factors that contribute to the popularity of CNC lathe machining. The automated nature of the process allows for faster production cycles, reducing lead times significantly. Additionally, the computerized controls enable manufacturers to operate multiple machines simultaneously, further improving efficiency and increasing production output.Another noteworthy advantage of CNC lathe machining is its versatility. This technology can be employed to manufacture parts for various industries, including automotive, aerospace, electronics, and medical. From engine components to intricate electronic circuits, CNC lathe machines have proven to be versatile enough to handle diverse manufacturing requirements.The increased automation in CNC lathe machining also leads to improved operational safety. As the need for manual intervention decreases, the risk of accidents and injuries is significantly reduced. This not only ensures the well-being of operators but also results in a safer working environment overall.Furthermore, CNC lathe machining offers enhanced consistency and repeatability. The computerized controls ensure that every part produced adheres to the specified design and dimensional requirements. This consistency is vital in industries where precision and conformity are paramount to product quality.With these advantages in mind, the company {} has emerged as a leading player in the CNC lathe machining market. Established in {}, {} has been at the forefront of innovating and delivering cutting-edge CNC lathe machines to various industries.The company's dedication to research and development has allowed them to push the boundaries of CNC lathe machining technology. By continuously improving their machines, they offer customers advanced features such as high spindle speed, faster tool changing capabilities, and improved automation, resulting in increased productivity and reduced production costs.Moreover, {}'s commitment to customer satisfaction is evident through their comprehensive support services. They provide training and guidance to their clients, ensuring they maximize the potential of the CNC lathe machines. Additionally, their dedicated after-sales service team ensures prompt and effective resolutions to any technical issues that may arise.In recognition of their contributions to the industry, {} has received numerous accolades and certifications for their CNC lathe machines. These achievements further solidify their position as a trusted and reliable provider of CNC lathe machining solutions.As the manufacturing industry continues to embrace automation and precision, CNC lathe machining is set to play an increasingly pivotal role. With its unparalleled accuracy, efficiency, and versatility, companies like {} are leading the charge in revolutionizing the way parts are manufactured. By harnessing the power of CNC lathe machining, businesses can stay competitive in today's fast-paced and evolving market.
Revolutionizing 3D Printing: A Closer Look at SLS Technology
[News Title]: Groundbreaking 3D Printing Technology Revolutionizes Manufacturing Industry[News Introduction]:In today's constantly evolving technological landscape, traditional manufacturing practices are being challenged by innovative and groundbreaking solutions. The advent of additive manufacturing, popularly known as 3D printing, has disrupted the industry by offering unparalleled efficiency, cost-effectiveness, and design possibilities. One of the frontrunners in this field, an emerging leader, is significantly transforming the way we think about manufacturing. Their innovative SLS printing technology has already begun revolutionizing various sectors by addressing key challenges and offering outstanding solutions.[Company Introduction]:The pioneering company, leveraging state-of-the-art manufacturing techniques and an impeccable understanding of industry needs, has emerged as an industry trailblazer. Founded on the principles of innovation, sustainability, and affordability, this cutting-edge organization has a track record of consistently pushing the boundaries of what is possible. Their SLS printing technology has gained widespread acclaim and recognition for its ability to transform complex designs into physical objects with stunning accuracy.[Background]:Traditional manufacturing processes often encounter limitations when it comes to creating intricate or customized designs. Conventional methods, such as injection molding or subtractive manufacturing, are time-consuming and costly. Prototyping and production can be resource-intensive, and the limitations tied to these techniques often hamper innovation and creativity. However, with the introduction of SLS printing, the game is set to change.[SLS Printing Revolutionizing Manufacturing]:SLS printing, short for Selective Laser Sintering, boasts several advantages over traditional manufacturing processes. Using powdered materials, such as plastics, metals, or ceramics, SLS printing creates three-dimensional objects by selectively fusing the powdered particles layer by layer. This process not only eliminates the need for expensive tooling but also unlocks endless possibilities for design complexity and customization.Furthermore, SLS printing enables the creation of structures with intricate internal geometries, making it ideal for producing lightweight components that would be impossible through traditional means. The technology's ability to print objects with moving parts or integrated functionalities amplifies its potential applications across various industries.In addition to its design flexibility, SLS printing also reduces waste compared to conventional manufacturing methods. By using only the necessary amount of raw material, it minimizes the ecological impact and material waste. Consequently, this groundbreaking technology aligns perfectly with the global shift towards sustainability and eco-friendly practices.[Applications and Impact]:The advent of SLS printing technology opens up exciting opportunities across multiple sectors. In the healthcare industry, medical professionals now have the ability to create custom implants tailored to individual patients, enhancing treatment outcomes and patient satisfaction. The aerospace industry benefits from lightweight yet structurally sound components, improving fuel efficiency and reducing emissions. Automotive manufacturers can now produce complex designs for customized parts and rapid prototyping, reducing production time and costs significantly.Moreover, SLS printing empowers creative designers and artists by translating their intricate visions into physical reality. Artists can now produce sculptures and intricate artworks that were once deemed impossible to fabricate. Architects can design and print detailed scale models, enabling better visualization and collaboration with clients.[Conclusion]:As the manufacturing industry embraces the innovation and potential of SLS printing, the possibilities for growth and development are immense. This revolutionary technology not only enhances design flexibility and efficiency but also contributes to creating a more sustainable and environmentally conscious future. With its continuous efforts in pushing the boundaries of what is possible, the company has established itself as a key player driving the 3D printing revolution. As industries across the globe adopt SLS printing, it can be anticipated that we are witnessing the dawn of a new era in manufacturing.
Discover the Benefits of Machining High-Quality Aluminum Parts
Title: Precision Engineering Company Expands Machining Capabilities with Aluminum Parts ProductionIntroduction:[Company Name], a pioneering name in the field of precision engineering, is proud to announce an expansion of its machining capabilities to include the production of high-quality aluminum parts. With a focus on cutting-edge technological solutions and a commitment to client satisfaction, [Company Name] aims to revolutionize the industry by offering a wide range of precision-machined aluminum components tailored to meet various industrial needs.Body:1. Growing Demand for Aluminum Parts:In response to the industry's growing demand for lightweight yet durable materials, [Company Name] recognizes the significance of aluminum as a widely preferred option. Known for its excellent mechanical properties and exceptional corrosion resistance, aluminum has become a go-to choice for industries ranging from aerospace and automotive to electronics and construction. By incorporating aluminum parts into its repertoire, [Company Name] aims to cater to the evolving needs of its diverse clientele, while also capturing new market segments.2. Cutting-Edge Machining Techniques:[Company Name] reinforces its commitment to excellence by employing state-of-the-art machining techniques to craft aluminum parts. Equipped with advanced CNC (Computer Numerical Control) machines and a highly-trained workforce, [Company Name] ensures precise and intricate manufacturing with consistent quality for every aluminum component produced. This dedication to precision allows for seamless integration of aluminum parts into various complex engineering systems.3. Broad Applications:The addition of aluminum parts to its product line allows [Company Name] to cater to a wide range of applications across different industries. From aerospace structural components, automotive engine parts, and electronic enclosures to architectural fittings and electrical connectors, the versatility of aluminum makes it an ideal choice for several demanding applications. [Company Name] aims to provide industry-leading solutions for these particular sectors by offering custom-designed aluminum parts that address both functional requirements and aesthetic considerations.4. Quality Assurance:Recognizing the importance of quality control, [Company Name] has implemented stringent quality assurance procedures throughout the aluminum parts manufacturing process. The company adheres to industry standards and regulations to ensure that each product meets or exceeds client expectations. Rigorous testing, dimensional verification, and surface treatments are carried out at every stage to guarantee impeccable craftsmanship, strength, and durability.5. Environmental Sustainability:In line with [Company Name]'s dedication to sustainability, the inclusion of aluminum parts in its production line helps reduce environmental impact. Aluminum is renowned for its recyclability, making it an eco-friendly alternative to many conventional materials. By introducing meticulously manufactured aluminum parts, [Company Name] supports the transition towards sustainable practices, providing clients with environmentally conscious solutions.6. Collaborative Approach and Design Customization:[Company Name] understands that each customer is unique, with specific design requirements and preferences. The company offers a collaborative approach to projects, ensuring effective communication between its engineering teams and clients. By actively involving clients in the design phase, [Company Name] ensures the production of customized aluminum parts that fulfill specific application demands, resulting in enhanced performance and optimized functionality.7. Streamlined Manufacturing and Timely Delivery:With its decades of experience in the precision engineering industry, [Company Name] emphasizes efficiency in manufacturing and timely delivery. The company's advanced production facilities, coupled with its optimized supply chain management, enables it to meet tight deadlines without compromising the quality of aluminum parts. [Company Name] aims to become a trusted partner, providing reliable solutions to clients around the world.Conclusion:As [Company Name] takes a step forward in expanding its machining capabilities to include aluminum parts production, it reaffirms its commitment to delivering cutting-edge engineering solutions. By combining advanced machining techniques, industry-leading quality standards, and a commitment to customer satisfaction, [Company Name] establishes itself as a premier provider of precision-machined aluminum components, meeting the evolving needs of industries across the board and contributing to a more sustainable future.
CNC Milling Shop: Unleashing the Potential of Precision Machining
CNC Milling Shop Embraces Advanced Technology to Cater to Growing Demands[City, Date] - In an era driven by technological advancements, businesses across various industries are continuously embracing cutting-edge solutions to stay ahead of the competition. One such establishment, the CNC Milling Shop, has taken significant strides in incorporating advanced technology to cater to the ever-growing demands of its clientele.With a commitment to delivering high-quality precision engineering solutions, the CNC Milling Shop has become a trusted name in the manufacturing sector. The company offers a diverse range of services including CNC milling, turning, and grinding, utilizing state-of-the-art machinery and tools, paired with skilled technicians to provide accurate and efficient results.The CNC Milling Shop has recently expanded its capabilities, investing in the latest CNC machines and software to further enhance their manufacturing processes. By incorporating Computer Numerical Control (CNC) technology, the shop has achieved increased precision, improved efficiency, and reduced production times.Leading the way in the industry, the CNC Milling Shop has established itself as a go-to destination for businesses seeking customized components and parts. Using their advanced software, they are able to convert complex designs into digital models, ensuring accuracy and consistency in the manufacturing process. This level of precision guarantees that the final product meets exact specifications, resulting in high customer satisfaction and repeat business.The company's commitment to quality extends beyond the use of advanced machinery. The CNC Milling Shop employs a team of highly skilled technicians who undergo regular training to stay up-to-date with the latest methods and best practices in the industry. The combination of their expertise and cutting-edge technology allows the shop to tackle complex projects with ease, no matter the size or intricacy.In addition to their focus on precision engineering, the CNC Milling Shop also prioritizes customer satisfaction. By providing excellent customer service and prompt delivery, they have built strong and lasting relationships with clients from a wide range of industries, including aerospace, automotive, medical, and electronics.The CNC Milling Shop understands the importance of adhering to stringent quality control standards. Their commitment to quality is reflected in their ISO 9001 certification, an internationally recognized standard for quality management systems. This certification guarantees that they meet the highest standards of quality and reliability in their products and services.Looking towards the future, the CNC Milling Shop has plans to further expand its operations and capabilities. The company aims to invest in cutting-edge technology, such as 5-axis machining, which will allow them to take on even more complex projects and provide greater design freedom to their clients.With an unwavering commitment to quality, advanced technology, and customer satisfaction, the CNC Milling Shop is poised to continue its growth and success in the precision engineering sector. Their dedication to staying ahead of the curve and embracing the latest innovations ensures that they remain a leader in the industry and a trusted partner for businesses seeking high-quality manufacturing solutions.About the CNC Milling Shop:The CNC Milling Shop is a leading precision engineering company specializing in CNC milling, turning, and grinding. With state-of-the-art machinery, cutting-edge software, and a highly skilled team of technicians, they provide accurate and efficient manufacturing solutions to clients across various industries.For media inquiries, please contact:Name: [Media Contact Name]Organization: [Company Name]Phone: [Contact Number]Email: [Contact Email]
Mastering the Art of 5 Axis CNC Milling: Unveiling the Pinnacle of Precision Engineering
Title: Innovations in 5-Axis CNC Milling Revolutionize Manufacturing ProcessIntroduction:(Company name), a prominent player in the manufacturing industry, continues to drive innovation and excellence through the introduction of their state-of-the-art 5-axis CNC milling machines. This cutting-edge technology is set to revolutionize the manufacturing process, offering enhanced precision, speed, and versatility for a wide range of industries. With their commitment to continually advancing manufacturing capabilities, (Company name) aims to optimize production efficiency, reduce costs, and deliver superior quality products, positioning themselves at the forefront of the industry.1. Exploring the Transformative Potential of 5-Axis CNC Milling:The advent of 5-axis CNC milling has brought a paradigm shift to the manufacturing industry. Unlike traditional 3-axis machines, 5-axis CNC milling machines have the capability to move and rotate the component in five directions simultaneously. This added flexibility enables manufacturers to produce complex and intricate components with exceptional precision, consistency, and efficiency.2. Unmatched Precision and Accuracy:The integration of advanced computer software and cutting-edge machine hardware within the 5-axis CNC milling system ensures unparalleled precision and accuracy. The ability to manipulate the tool in multiple axes eliminates the need for repositioning, therefore reducing human error and enhancing precision. This level of accuracy ensures that even the most complex parts are machined with utmost precision, resulting in improved product quality and reduced wastage.3. Enhanced Versatility and Flexibility:The 5-axis CNC milling machines provided by (Company name) offer enhanced versatility and flexibility compared to conventional machining methods. The ability to manipulate the component from various angles enables the production of highly intricate and complex geometries in a single setup. This eliminates the need for multiple machines or operations and streamlines the production process, significantly reducing lead times and costs.4. Improved Efficiency and Productivity:By integrating 5-axis CNC milling into their manufacturing processes, businesses can witness significant improvements in efficiency and productivity. The simultaneous movements in multiple axes enable the machines to complete complex operations in a single cycle, reducing production time and increasing throughput. Additionally, the machines can operate continuously, minimizing downtime and translating into increased productivity and profitability for manufacturing businesses.5. Cost-Effective Manufacturing:The utilization of 5-axis CNC milling machines by (Company name) translates into cost-effective manufacturing for businesses. With the ability to produce complex components in a single setup, manufacturers can save on labor costs, materials, and machine investments. Furthermore, the enhanced precision and accuracy of the machines minimize the occurrence of errors and rework, resulting in further cost savings.6. Expanding Applications across Industries:The applications of 5-axis CNC milling machines extend across a wide range of industries, including aerospace, automotive, medical, and energy sectors. The technology enables manufacturers to tackle complex tasks such as prototyping, mold making, and part manufacturing, with unparalleled precision. Its versatility and flexibility make it ideal for industries requiring the production of intricate parts or customized components.7. (Company name) Leading the Way:(Company name) has positioned itself as a pioneering force in the 5-axis CNC milling domain. With a focus on continuous innovation and unparalleled customer support, (Company name) exemplifies its commitment to spearheading technological advancements in the industry. By partnering with world-class engineers and researchers, (Company name) aims to push the boundaries of performance and reliability, ensuring their customers stay ahead of the competition.Conclusion:The introduction of 5-axis CNC milling machines by (Company name) marks a significant milestone in the manufacturing industry. The combination of precision, accuracy, versatility, and efficiency offers manufacturers an opportunity to enhance their product quality, reduce costs, and stay ahead in a highly competitive market. As the industry-leading player, (Company name) continues to set new standards in machining technology and remains dedicated to driving innovation to shape the future of manufacturing.
Unveiling the Latest Innovations and Advancements in CNC Metalworking
CNC Metalworking Continues to Revolutionize the Manufacturing IndustryIn the fast-paced world of manufacturing, precision and efficiency are key. One company has been at the forefront of revolutionizing the industry by utilizing CNC metalworking technology to create high-quality products with speed and accuracy. With their cutting-edge machinery and dedication to innovation, this company is poised to lead the way into the future of manufacturing.Founded in 1995, this company has been a driving force in the CNC metalworking industry for over two decades. With their state-of-the-art facilities and highly skilled technicians, they have been able to consistently deliver exceptional results to their clients. By investing in the latest advancements in CNC machining technology, they have been able to streamline production processes and enhance product quality.One of the biggest advantages of CNC metalworking is its ability to manufacture intricate parts with unparalleled precision. This level of accuracy ensures that each component produced meets the strictest quality standards. Gone are the days of human error and inconsistency. CNC machines can replicate designs with absolute fidelity, resulting in flawless and reliable products every time.Furthermore, CNC metalworking significantly reduces production time. With traditional methods, manufacturing even a simple part could take days or even weeks. However, with the implementation of CNC machinery, the time required to produce complex components has been drastically reduced. This accelerated turnaround time allows businesses to meet consumer demands more efficiently and stay ahead of their competition.The benefits of CNC metalworking extend beyond precision and speed. This manufacturing process also offers a range of material options to choose from. With the ability to work with various metals such as aluminum, stainless steel, and titanium, this company is able to cater to a wide array of industries and their unique requirements. From aerospace to automotive, medical to electronics, their CNC metalworking capabilities are limitless.Additionally, CNC metalworking is highly cost-effective. By automating the production process, this company can minimize labor costs and reduce material waste. With skilled technicians operating the CNC machines, errors are minimized, resulting in fewer defective parts. This not only saves time and money but also ensures that quality standards are consistently met.Furthermore, CNC metalworking eliminates the need for retooling between different jobs. Changing from one product to another in traditional manufacturing often required extensive setup and reconfiguration of the machinery. However, CNC machines can easily switch between jobs without any significant downtime. This flexibility allows for improved efficiency and increased production capacity.In order to stay at the forefront of the CNC metalworking industry, this company continually invests in research and development. By keeping a close eye on emerging technologies and trends, they can adapt and integrate the latest advancements into their production processes. This commitment to innovation ensures that they remain ahead of their competition and continue to offer cutting-edge solutions to their clients.As the manufacturing industry continues to evolve, CNC metalworking will undoubtedly play a crucial role in shaping its future. With its combination of precision, efficiency, and versatility, this technology is revolutionizing the way products are made. This company's dedication to excellence and their adoption of CNC metalworking continues to set new standards in the manufacturing industry.In conclusion, this renowned company has truly made a mark in the CNC metalworking industry. Their commitment to precision, efficiency, and innovation has allowed them to create superior products that meet the demanding requirements of various industries. With their state-of-the-art facilities and highly skilled technicians, they are well-positioned to continue leading the way in CNC metalworking. As the manufacturing industry moves forward, this company's dedication to excellence ensures that they will remain at the forefront of innovation and continue to shape the future of manufacturing.
Top Prototyping Companies in the United States: Your Go-To Guide for Successful Prototyping Projects
[Company Introduction - Remove Brand Name][Company Name], a leading prototyping company based in the United States, is revolutionizing the manufacturing industry with its innovative approach. With a dedicated team of experts and state-of-the-art facilities, [Company Name] offers a wide range of prototyping services to cater to the diverse needs of its clients.Established several years ago, [Company Name] has quickly gained a reputation for delivering high-quality prototypes with exceptional precision and efficiency. The company takes pride in its ability to bring clients' ideas to life, assisting them in transforming concepts into tangible products that can be tested and validated before entering full-scale production.At the heart of [Company Name]'s success lies its commitment to utilizing the latest advancements in technology. Equipped with cutting-edge machinery and software, the company is capable of producing prototypes with intricate details and intricate components. This ensures that clients receive prototypes that are not only visually appealing but also functionally robust.One of the key strengths of [Company Name] is its diverse range of prototyping capabilities. The company specializes in various prototyping methods, including 3D printing, CNC machining, vacuum casting, and injection molding. This versatility allows [Company Name] to adapt to different project requirements, whether it be for rapid prototyping, functional testing, or low-volume production.Furthermore, [Company Name]'s team of skilled engineers and designers play a vital role in the prototyping process. With their expertise and experience, they collaborate closely with clients, offering valuable insights and recommendations to optimize the design and functionality of the prototypes. This collaborative approach ensures that the final product meets the exact specifications and requirements of the client.In addition to their prototyping services, [Company Name] also provides a range of secondary services such as surface finishing, assembly, and packaging. This comprehensive approach allows clients to receive fully functional prototypes that closely resemble the final product.To cater to a wide range of industries, [Company Name] has developed expertise in prototyping for automotive, aerospace, consumer electronics, medical devices, and many other sectors. The company understands the unique challenges and regulations that each industry presents and ensures adherence to the highest quality standards.One of the key factors that sets [Company Name] apart from its competitors is its dedication to customer satisfaction. The company prides itself on its prompt and reliable service, ensuring a smooth and seamless prototyping experience for clients. From the initial consultation to the final delivery, [Company Name] places great emphasis on clear communication, attention to detail, and meeting project deadlines.With a growing portfolio of successful projects and satisfied clients, [Company Name] continues to establish itself as a leader in the prototyping industry. By investing in research and development, staying up-to-date with emerging technologies, and fostering a culture of innovation, the company is well-positioned to shape the future of prototyping.In conclusion, [Company Name] is a prototyping company based in the United States that is leading the way in revolutionizing the manufacturing industry. With its state-of-the-art facilities, diverse range of capabilities, and commitment to customer satisfaction, [Company Name] is adept at turning clients' ideas into tangible products through high-quality prototypes. With their dedication to innovation and exceptional service, [Company Name] is poised to remain at the forefront of the prototyping industry for years to come.
CNC Lathe Process: Streamlining Precision Machining Operations
Title: Innovations in CNC Lathe Process Revolutionize Manufacturing IndustryIntroduction:The manufacturing industry has witnessed a groundbreaking technological advancement with the introduction of the new CNC Lathe Process. Spearheaded by the pioneering efforts of various companies, including {}, this cutting-edge technology promises to revolutionize productivity, precision, and efficiency. By eliminating the need for manual operation and introducing automated capabilities, CNC Lathe Process has successfully overcome conventional limitations and opened new doors for manufacturers worldwide.Improved Precision and Accuracy:One of the key advantages of the CNC Lathe Process is its ability to achieve unmatched precision and accuracy in machining operations. Through the integration of advanced computer-controlled systems, {} has developed a CNC Lathe that can execute intricate tasks with exceptional detail. This eliminates human error and allows for consistent and repeatable results, ensuring the highest quality of machined components. With this level of precision, manufacturers can enhance their product offerings, meeting the ever-increasing demands of modern consumers.Enhanced Efficiency and Productivity:By automating the manufacturing process, CNC Lathe Process has significantly improved efficiency and productivity. {} has strived to optimize their CNC Lathes' operational speed, enabling faster turnaround times and increased output. The utilization of CNC technology eliminates the need for manual intervention, thereby reducing idle time between operations. Moreover, the integration of advanced software and algorithms allows for seamless multitasking, as the CNC Lathe can perform various complex operations simultaneously. As a result, manufacturers can save valuable time and resources, ultimately boosting their bottom line.Versatility and Flexibility:The flexibility offered by the CNC Lathe Process has opened up new avenues for manufacturers seeking to diversify their product range. With the ability to program the CNC Lathe to perform different operations, {} ensures that manufacturers have the flexibility to produce a wide range of components. This flexibility not only allows for process streamlining and optimization but also provides businesses with a competitive edge in the market. CNC Lathe Process enables manufacturers to adapt quickly to changing customer demands and produce complex components with ease.Cost-effective Manufacturing:The implementation of CNC Lathe Process has proven to be cost-effective in the long run. While the initial investment may be higher compared to traditional machining methods, the return on investment is significant. By reducing reliance on manual labor, companies can optimize workforce allocation and reduce labor costs. Furthermore, the accuracy and precision achieved by CNC Lathe Process result in minimal material wastage, reducing production costs. This cost-effectiveness translates into a competitive advantage for manufacturers, allowing them to offer competitive pricing while maintaining profitability.Consistency and Quality Control:CNC Lathe Process ensures consistency and stringent quality control throughout the production cycle. The computer-controlled systems developed by {} continuously monitor and adjust machining parameters, guaranteeing that every component produced adheres to the specified standards. Consistent quality control minimizes the risk of defects and rejects, thereby enhancing customer satisfaction. Manufacturers can confidently deliver high-quality components, boosting their reputation and gaining a competitive edge in the market.Conclusion:The introduction of CNC Lathe Process has revolutionized the manufacturing industry, elevating productivity, precision, and efficiency to unprecedented heights. {} has played a significant role in shaping this technological advancement, with their innovative CNC Lathe technology. The advantages of CNC Lathe Process, including improved precision, enhanced efficiency, flexibility, cost-effectiveness, and consistent quality control, position manufacturers to thrive in the highly competitive global market. As the manufacturing industry embraces this transformative technology, we can anticipate further advancements and a future characterized by limitless possibilities.