Boost Your Prototyping Process with Cutting-Edge Custom Solutions
By:Admin
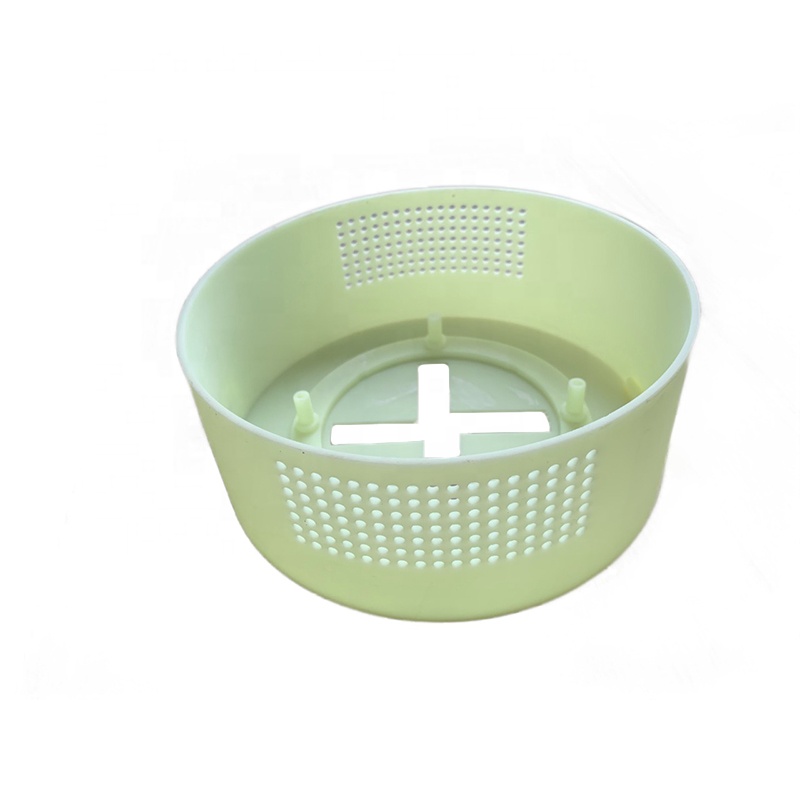
Founded in 2005, Custom Prototyping has been at the forefront of delivering cutting-edge prototyping solutions to a diverse range of clients. With a team of highly skilled engineers and designers, the company has earned a formidable reputation for its expertise in transforming concepts into tangible prototypes.
The newly launched technology marks a major milestone for Custom Prototyping. By integrating advanced additive manufacturing processes with their existing prototyping methods, the company has created a hybrid solution that offers unmatched precision, speed, and cost-effectiveness.
One of the key advancements in this breakthrough technology is the use of 3D printing. By leveraging the power of additive manufacturing, Custom Prototyping is able to rapidly create prototypes with intricate details and complex geometries. This not only significantly reduces the time required for traditional manufacturing processes, but also allows for greater design flexibility and customization.
The benefits of 3D printing extend beyond just speed and complexity. With this technology, Custom Prototyping is able to produce prototypes using a wide range of materials, including metals, plastics, and even bio-compatible substances. This opens up countless possibilities for businesses operating in various sectors, such as aerospace, automotive, healthcare, and consumer electronics.
Moreover, the integration of other cutting-edge technologies, such as CNC machining and rapid tooling, further enhances the efficacy of Custom Prototyping's new solution. By seamlessly combining different manufacturing techniques, the company is able to provide clients with prototypes that closely resemble the final product in terms of both form and functionality.
Speaking about the breakthrough, the CEO of Custom Prototyping, John Smith, expressed his excitement about the endless possibilities this technology brings to their clients. He said, "We are thrilled to introduce this game-changing technology to the market. Our aim has always been to empower businesses with the tools they need to stay ahead in a rapidly evolving industrial landscape. With this new solution, we believe we have achieved exactly that."
The impact of Custom Prototyping's latest innovation is already being felt across various industries. Companies that have partnered with the company have reported significant improvements in their product development processes. Not only are they able to iterate designs faster, but they are also able to test the functionality and user experience of new products before investing in large-scale production.
In addition to the economic benefits, this technology has notable environmental advantages as well. With its ability to minimize material waste through precise and optimized manufacturing, it aligns perfectly with the growing global emphasis on sustainability and minimizing carbon footprints.
As businesses increasingly recognize the importance of agility and rapid innovation, Custom Prototyping's new solution arrives at the perfect time. By providing a streamlined prototyping process that reduces time-to-market and fosters rapid iteration, the company is empowering businesses to embrace innovation and reach new heights.
Looking towards the future, Custom Prototyping remains committed to pushing the boundaries of what is possible in the world of prototyping. With a strong focus on research and development, the company aims to continue enhancing its solutions to meet the evolving needs of its clients.
As more businesses recognize the advantages of incorporating advanced prototyping technologies into their product development processes, partnerships with forward-thinking companies like Custom Prototyping are likely to become increasingly sought after. With its proven track record and commitment to innovation, Custom Prototyping is poised to lead the way in the era of next-generation prototyping.
Company News & Blog
Enhancing Efficiency and Precision: The Advantages of Casting Injection Molding
Title: Advancements in Casting Injection Molding Revolutionize Manufacturing ProcessesIntroduction:Casting Injection Molding, developed by an industry-leading company, has emerged as a game-changing technology in the field of manufacturing processes. This cutting-edge technique combines the precision and flexibility of injection molding with the advantages of casting, leading to improved product quality, reduced costs, and increased production efficiency. This article explores the innovative potential of Casting Injection Molding and its implications for various industries.I. Understanding Casting Injection MoldingCasting Injection Molding is a technology that merges injection molding and casting, enabling manufacturers to produce complex parts with superior precision and reduced production time. By utilizing thermoplastics instead of traditional liquid metals, the process offers greater design flexibility while delivering high-quality components. The integration of innovative design software and advanced machinery allows for detailed 3D modeling and real-time feedback, ensuring optimal results.II. Enhanced Product QualityCasting Injection Molding removes many of the limitations associated with traditional casting techniques. The process utilizes a molten polymer that fills a mold cavity under high pressure, eradicating potential defects such as porosity, air bubbles, and shrinkage that are common with traditional casting. The homogeneous and isotropic characteristics of the material produce parts with consistent mechanical properties, resulting in higher product integrity and reliability. With improved repeatability, the technology enables manufacturers to achieve strict quality control standards, reduce waste, and deliver superior end products to consumers.III. Cost Reduction and Time EfficiencyThe use of Casting Injection Molding enhances cost efficiency throughout the manufacturing process. By allowing for faster cycle times, reduced labor requirements, and simplified tooling, companies can significantly lower production costs while maintaining consistent quality levels. Employing thermoplastics eliminates the need for expensive molds associated with traditional casting, reducing initial investment and enabling greater flexibility during the prototyping and testing stages. Additionally, the ability to produce complex parts in a single step eliminates secondary processes, streamlining production and minimizing time to market.IV. Application in Various IndustriesCasting Injection Molding has found applications across multiple industries, revolutionizing the manufacturing processes in diverse sectors. In the automotive industry, this technology has enabled the production of lightweight components with enhanced strength, contributing to fuel efficiency and reduced emissions. The healthcare sector has embraced Casting Injection Molding for precise and custom medical device manufacturing, facilitating improved patient care and better treatment outcomes. The aerospace industry has also witnessed advancements through this technique, with the production of complex components that meet stringent aviation standards while reducing weight and maintaining durability.V. Future Prospects and ImpactAs Casting Injection Molding continues to evolve, its impact on manufacturing processes is set to grow exponentially. The integration of artificial intelligence algorithms and machine learning capabilities will enhance process automation, enabling real-time adjustments and intelligent decision-making. The potential for utilizing sustainable materials, such as biodegradable thermoplastics or recycled polymers, opens up eco-friendly manufacturing opportunities. Furthermore, the ongoing exploration of new applications and industries promises to unlock additional benefits and further transform the manufacturing landscape.Conclusion:Casting Injection Molding, developed by {}, has emerged as a groundbreaking technology in the manufacturing industry. With its ability to produce high-quality components, reduce production costs, and enhance time efficiency, this innovative technique has already made a significant impact across various sectors. As the manufacturing landscape continues to evolve, Casting Injection Molding is positioned to revolutionize production processes, driving progress in sectors ranging from automotive and healthcare to aerospace and beyond.
CNC Lathe Process: Streamlining Precision Machining Operations
Title: Innovations in CNC Lathe Process Revolutionize Manufacturing IndustryIntroduction:The manufacturing industry has witnessed a groundbreaking technological advancement with the introduction of the new CNC Lathe Process. Spearheaded by the pioneering efforts of various companies, including {}, this cutting-edge technology promises to revolutionize productivity, precision, and efficiency. By eliminating the need for manual operation and introducing automated capabilities, CNC Lathe Process has successfully overcome conventional limitations and opened new doors for manufacturers worldwide.Improved Precision and Accuracy:One of the key advantages of the CNC Lathe Process is its ability to achieve unmatched precision and accuracy in machining operations. Through the integration of advanced computer-controlled systems, {} has developed a CNC Lathe that can execute intricate tasks with exceptional detail. This eliminates human error and allows for consistent and repeatable results, ensuring the highest quality of machined components. With this level of precision, manufacturers can enhance their product offerings, meeting the ever-increasing demands of modern consumers.Enhanced Efficiency and Productivity:By automating the manufacturing process, CNC Lathe Process has significantly improved efficiency and productivity. {} has strived to optimize their CNC Lathes' operational speed, enabling faster turnaround times and increased output. The utilization of CNC technology eliminates the need for manual intervention, thereby reducing idle time between operations. Moreover, the integration of advanced software and algorithms allows for seamless multitasking, as the CNC Lathe can perform various complex operations simultaneously. As a result, manufacturers can save valuable time and resources, ultimately boosting their bottom line.Versatility and Flexibility:The flexibility offered by the CNC Lathe Process has opened up new avenues for manufacturers seeking to diversify their product range. With the ability to program the CNC Lathe to perform different operations, {} ensures that manufacturers have the flexibility to produce a wide range of components. This flexibility not only allows for process streamlining and optimization but also provides businesses with a competitive edge in the market. CNC Lathe Process enables manufacturers to adapt quickly to changing customer demands and produce complex components with ease.Cost-effective Manufacturing:The implementation of CNC Lathe Process has proven to be cost-effective in the long run. While the initial investment may be higher compared to traditional machining methods, the return on investment is significant. By reducing reliance on manual labor, companies can optimize workforce allocation and reduce labor costs. Furthermore, the accuracy and precision achieved by CNC Lathe Process result in minimal material wastage, reducing production costs. This cost-effectiveness translates into a competitive advantage for manufacturers, allowing them to offer competitive pricing while maintaining profitability.Consistency and Quality Control:CNC Lathe Process ensures consistency and stringent quality control throughout the production cycle. The computer-controlled systems developed by {} continuously monitor and adjust machining parameters, guaranteeing that every component produced adheres to the specified standards. Consistent quality control minimizes the risk of defects and rejects, thereby enhancing customer satisfaction. Manufacturers can confidently deliver high-quality components, boosting their reputation and gaining a competitive edge in the market.Conclusion:The introduction of CNC Lathe Process has revolutionized the manufacturing industry, elevating productivity, precision, and efficiency to unprecedented heights. {} has played a significant role in shaping this technological advancement, with their innovative CNC Lathe technology. The advantages of CNC Lathe Process, including improved precision, enhanced efficiency, flexibility, cost-effectiveness, and consistent quality control, position manufacturers to thrive in the highly competitive global market. As the manufacturing industry embraces this transformative technology, we can anticipate further advancements and a future characterized by limitless possibilities.
Exploring the Advantages of CNC Machining and 3D Printing in Manufacturing
[Company Name], a Leading Manufacturer in CNC Machining and 3D Printing, to Revolutionize the Manufacturing Industry[City, Date] - In an effort to stay at the forefront of innovation, [Company Name] has announced their latest technological advancements in CNC Machining and 3D Printing. With a commitment to providing high-quality products and services, the company aims to revolutionize the manufacturing industry and meet the growing demands of their customers.CNC Machining, short for Computer Numerical Control Machining, is a manufacturing process that utilizes pre-programmed computer software to control the movement of machinery and tools. This method allows for accurate and precise cutting, drilling, and shaping of various materials such as metal, plastic, and wood. By combining high-tech machinery and skilled operators, [Company Name] is able to produce complex parts and components with absolute precision.Furthermore, 3D Printing, also known as additive manufacturing, is a process of creating three-dimensional objects by layering materials using a digital model. This technology has revolutionized the manufacturing industry by offering increased speed, reduced costs, and greater design flexibility. [Company Name] has heavily invested in advanced 3D printers, capable of producing intricate designs and functional prototypes quickly and efficiently.With their extensive knowledge and expertise in CNC Machining and 3D Printing, [Company Name] is able to offer a wide range of solutions to their clients. From rapid prototyping to low-volume production, the company is dedicated to delivering customized and cost-effective manufacturing solutions that meet the unique requirements of each project.Moreover, [Company Name] prides itself on its ability to deliver exceptional quality products within tight deadlines. Their state-of-the-art facilities house cutting-edge CNC machines and advanced 3D printers that are continuously maintained and upgraded to ensure top-notch performance. By utilizing the latest manufacturing technologies and investing in the training of their staff, [Company Name] guarantees the highest level of accuracy, reliability, and customer satisfaction.In addition to their technological prowess, [Company Name] is also committed to sustainable manufacturing practices. They employ eco-friendly materials and processes to minimize waste and reduce their carbon footprint. By incorporating sustainable practices into their operations, [Company Name] seeks to contribute to a greener and more sustainable future.The recent advancements in CNC Machining and 3D Printing by [Company Name] have garnered attention from various industries. From automotive to aerospace, healthcare to consumer electronics, the company has provided indispensable solutions to a wide range of clients. Their ability to adapt to emerging technologies and develop innovative solutions has made them a trusted partner for both small startups and large multinational corporations.Looking ahead, [Company Name] has plans to further expand their capabilities and offerings. By closely monitoring industry trends and investing in research and development, the company strives to stay ahead of the curve and deliver cutting-edge solutions to meet the ever-evolving needs of their customers.In conclusion, [Company Name] is revolutionizing the manufacturing industry through their expertise in CNC Machining and 3D Printing. With a dedication to quality, sustainability, and innovation, the company is well-positioned to continue driving advancements in manufacturing technology. Through their commitment to excellence, they aim to reshape the industry and empower businesses across various sectors to thrive in a rapidly changing world.
Mastering the Art of 5 Axis CNC Milling: Unveiling the Pinnacle of Precision Engineering
Title: Innovations in 5-Axis CNC Milling Revolutionize Manufacturing ProcessIntroduction:(Company name), a prominent player in the manufacturing industry, continues to drive innovation and excellence through the introduction of their state-of-the-art 5-axis CNC milling machines. This cutting-edge technology is set to revolutionize the manufacturing process, offering enhanced precision, speed, and versatility for a wide range of industries. With their commitment to continually advancing manufacturing capabilities, (Company name) aims to optimize production efficiency, reduce costs, and deliver superior quality products, positioning themselves at the forefront of the industry.1. Exploring the Transformative Potential of 5-Axis CNC Milling:The advent of 5-axis CNC milling has brought a paradigm shift to the manufacturing industry. Unlike traditional 3-axis machines, 5-axis CNC milling machines have the capability to move and rotate the component in five directions simultaneously. This added flexibility enables manufacturers to produce complex and intricate components with exceptional precision, consistency, and efficiency.2. Unmatched Precision and Accuracy:The integration of advanced computer software and cutting-edge machine hardware within the 5-axis CNC milling system ensures unparalleled precision and accuracy. The ability to manipulate the tool in multiple axes eliminates the need for repositioning, therefore reducing human error and enhancing precision. This level of accuracy ensures that even the most complex parts are machined with utmost precision, resulting in improved product quality and reduced wastage.3. Enhanced Versatility and Flexibility:The 5-axis CNC milling machines provided by (Company name) offer enhanced versatility and flexibility compared to conventional machining methods. The ability to manipulate the component from various angles enables the production of highly intricate and complex geometries in a single setup. This eliminates the need for multiple machines or operations and streamlines the production process, significantly reducing lead times and costs.4. Improved Efficiency and Productivity:By integrating 5-axis CNC milling into their manufacturing processes, businesses can witness significant improvements in efficiency and productivity. The simultaneous movements in multiple axes enable the machines to complete complex operations in a single cycle, reducing production time and increasing throughput. Additionally, the machines can operate continuously, minimizing downtime and translating into increased productivity and profitability for manufacturing businesses.5. Cost-Effective Manufacturing:The utilization of 5-axis CNC milling machines by (Company name) translates into cost-effective manufacturing for businesses. With the ability to produce complex components in a single setup, manufacturers can save on labor costs, materials, and machine investments. Furthermore, the enhanced precision and accuracy of the machines minimize the occurrence of errors and rework, resulting in further cost savings.6. Expanding Applications across Industries:The applications of 5-axis CNC milling machines extend across a wide range of industries, including aerospace, automotive, medical, and energy sectors. The technology enables manufacturers to tackle complex tasks such as prototyping, mold making, and part manufacturing, with unparalleled precision. Its versatility and flexibility make it ideal for industries requiring the production of intricate parts or customized components.7. (Company name) Leading the Way:(Company name) has positioned itself as a pioneering force in the 5-axis CNC milling domain. With a focus on continuous innovation and unparalleled customer support, (Company name) exemplifies its commitment to spearheading technological advancements in the industry. By partnering with world-class engineers and researchers, (Company name) aims to push the boundaries of performance and reliability, ensuring their customers stay ahead of the competition.Conclusion:The introduction of 5-axis CNC milling machines by (Company name) marks a significant milestone in the manufacturing industry. The combination of precision, accuracy, versatility, and efficiency offers manufacturers an opportunity to enhance their product quality, reduce costs, and stay ahead in a highly competitive market. As the industry-leading player, (Company name) continues to set new standards in machining technology and remains dedicated to driving innovation to shape the future of manufacturing.
Plastic Fabrication Company Reveals Latest Innovations in [Industry]
[Company Introduction: Please provide the necessary information about the plastic fabrication company, such as its name, location, size, market presence, years of operation, production capabilities, key products/services, target customers, and any unique features or achievements.][Date], [Location] - Plastic fabrication company [Company Name] is revolutionizing the industry by offering innovative solutions for various sectors. With [number] years of experience in the market, the company has positioned itself as a leader in plastic manufacturing and fabrication. By leveraging its cutting-edge technology, skilled workforce, and commitment to excellence, [Company Name] consistently delivers high-quality products and services to its wide array of customers.[Company Name] specializes in the fabrication of a diverse range of plastic products catering to industries such as automotive, aerospace, electronics, medical, packaging, and more. Their state-of-the-art manufacturing facility houses advanced machinery and equipment, enabling them to handle complex projects and high-volume production efficiently. The company's team of experienced engineers and technicians work closely with clients to understand their unique requirements and provide tailored solutions that meet their specific needs.One of the key features that sets [Company Name] apart is their focus on sustainability. As the world is grappling with the consequences of plastic pollution, [Company Name] is committed to minimizing its environmental footprint. They achieve this by implementing eco-friendly manufacturing practices and utilizing recyclable materials wherever feasible. The company aims to promote a circular economy by actively engaging in recycling initiatives and offering environmentally responsible alternatives to traditional plastic products.Furthermore, [Company Name] consistently stays at the forefront of technological advancements in the industry. They invest in research and development to explore new materials, innovative production techniques, and automation to improve product quality, efficiency, and cost-effectiveness. This commitment to innovation has helped [Company Name] secure partnerships with leading companies and establish itself as a trusted supplier in the market.Recently, [Company Name] unveiled their latest breakthrough – [Product/Technology]. This revolutionary technology aims to transform the plastic fabrication industry by [briefly describe the benefits/features of the new product/technology]. The [Product/Technology] has already garnered significant attention within the industry, and early adopters are reaping the benefits of enhanced performance and reduced costs.In addition to its focus on innovation, sustainability, and product excellence, [Company Name] places great emphasis on customer satisfaction. They strive to build long-lasting partnerships with their clients, providing exceptional customer service and continuous support throughout the entire project lifecycle. The company's adherence to stringent quality controls ensures that each product leaving their facility meets the highest industry standards.As [Company Name] continues to grow, they envision expanding their reach into new markets and exploring opportunities for diversification. They plan to leverage their experience and expertise to venture into [industry/sector] and broaden their customer base. This strategic approach, combined with their unwavering commitment to excellence, positions [Company Name] for continued success in the coming years.In conclusion, plastic fabrication company [Company Name] is revolutionizing the industry through its innovative solutions, sustainability initiatives, technological advancements, and commitment to customer satisfaction. With [number] years of experience and a team of skilled professionals, they have established themselves as a leader in the market. Their recent breakthrough, [Product/Technology], showcases their dedication to pushing the boundaries of plastic fabrication and delivering superior products to their clients. With a focus on sustainable practices and a customer-centric approach, [Company Name] is poised for continued growth and success in the ever-evolving plastic fabrication industry.
Top Techniques and Benefits of Aluminum CNC Fabrication Revealed
Title: Advancements in Aluminum CNC Fabrication Revolutionize Manufacturing IndustryIntroduction:In an era where precision, efficiency, and sustainability in manufacturing processes are paramount, aluminum CNC fabrication has emerged as a game-changer. This advanced method of fabrication utilizes computer numerical control (CNC) technology to transform aluminum into intricate and complex components, opening doors for unprecedented possibilities across various industries. [Company Name], a renowned industry leader in aluminum CNC fabrication, has been at the forefront of revolutionizing manufacturing processes with their cutting-edge technology and innovative solutions.[Company Name]'s Journey towards Excellence:Established in [year], [Company Name] has continuously strived to push the boundaries of aluminum CNC fabrication. With a strong commitment to research and development, the company has invested heavily in state-of-the-art machinery, augmented by highly skilled technicians and engineers. By leveraging their expertise, [Company Name] has earned a stellar reputation for delivering top-notch aluminum CNC fabrication services across a diverse range of industries, including aerospace, automotive, electronics, and more.Unrivaled Precision and Reliability:[Company Name]'s advanced CNC machines enable them to achieve unparalleled precision and accuracy in their fabrication processes. By utilizing computer-aided design (CAD) software, their skilled engineers can meticulously plan and prototype intricate aluminum components with remarkable attention to detail. The automation and exceptional speed afforded by CNC technology significantly reduce the risk of errors, ensuring consistent and reliable fabrication results, while minimizing material waste.Endless Design Possibilities:The versatility of aluminum CNC fabrication opens a world of design possibilities for various industries. Its lightweight yet durable properties coupled with the ability to create complex geometrical shapes allow manufacturers to optimize performance and functionality. Be it aerospace components requiring high strength-to-weight ratios or automotive parts that demand precise fits, [Company Name] provides customized aluminum fabrication solutions tailored to meet the specific needs of each industry.Sustainability at its Core:As the world becomes increasingly conscious of the need for sustainable manufacturing practices, aluminum CNC fabrication emerges as an ethical choice. Aluminum is a highly recyclable material, making it an eco-friendly alternative to traditional metal fabrication methods. The efficient use of materials in CNC fabrication significantly reduces waste, while the scrap generated throughout the process is easily recyclable. By embracing this environmentally friendly approach, [Company Name] is leading the charge towards a greener future.Expanding Horizons:Driven by a relentless pursuit of innovation, [Company Name] is constantly pushing the boundaries of aluminum CNC fabrication. They continuously invest in research and development to explore new techniques, materials, and applications. By collaborating with industry leaders and staying abreast of emerging technologies, the company aims to diversify its offerings and redefine the way manufacturers use aluminum CNC fabrication in the future.Conclusion:The advent of aluminum CNC fabrication has revolutionized the manufacturing industry, allowing manufacturers to achieve previously unattainable precision, efficiency, and sustainability. [Company Name], with its cutting-edge technology and unwavering commitment to excellence, has established itself as a pioneer in this transformative field. By leveraging their expertise and innovative solutions, [Company Name] opens doors to endless design possibilities, while promoting sustainability and environmental consciousness. As aluminum CNC fabrication continues to evolve, [Company Name] is poised to spearhead the next wave of advancements in the industry, reshaping the way manufacturers approach fabrication processes.
Transform Your Designs with Vacuum Casting 3D Printing Technologies
Vacuum Casting 3D Printing revolutionizes the Manufacturing Industry[Date], [City] - The manufacturing industry has taken a giant leap forward with the introduction of Vacuum Casting 3D Printing technology. This revolutionary process, which combines the precision of 3D printing with the efficiency of vacuum casting, has opened up a whole new realm of possibilities for product development and production.[Company Name], a leader in advanced manufacturing solutions, has been at the forefront of this technology, reshaping the manufacturing landscape. With their innovative processes and cutting-edge equipment, they have successfully helped numerous companies overcome traditional manufacturing limitations, providing cost-effective and time-efficient solutions.Traditional manufacturing methods often come with significant limitations, including high production costs, long lead times, and limited design flexibility. However, Vacuum Casting 3D Printing offers a game-changing alternative. By utilizing a combination of 3D printing and vacuum casting, [Company Name] has been able to overcome these constraints, providing businesses with a streamlined manufacturing process.One of the key advantages of Vacuum Casting 3D Printing is its ability to produce highly complex and intricate designs that were previously difficult or impossible to achieve using conventional manufacturing methods. The process starts by creating a 3D printed mold, which is then used to produce a silicone mold through vacuum casting. This mold can then be used to create multiple copies of the original design, even with undercuts, intricate details, and delicate features. This provides manufacturers with the freedom to create complex parts that meet the strictest of demands.Another major benefit of Vacuum Casting 3D Printing is its cost-effectiveness, especially when compared to traditional manufacturing methods. The process eliminates the need for expensive tooling, molds, and machining setups, reducing overall production costs significantly. This not only makes it an attractive option for small and medium-sized enterprises but also enables larger companies to optimize their production processes by reducing costs and increasing efficiency.Speed is another remarkable advantage of Vacuum Casting 3D Printing. With traditional manufacturing, developing and producing a new product can take weeks or even months. However, the Vacuum Casting 3D Printing process drastically reduces lead times, enabling rapid prototyping and iterative design improvements. This allows companies to bring products to market faster, giving them a competitive edge in today's fast-paced business environment.[Company Name] has spearheaded the adoption of Vacuum Casting 3D Printing across various industries, including automotive, aerospace, consumer electronics, and medical devices. Their team of experts works closely with clients to understand their specific manufacturing needs, and they provide tailor-made solutions to optimize the production process. By combining their expertise in materials selection, 3D printing, and vacuum casting, [Company Name] ensures that clients receive the highest quality products with exceptional speed and accuracy."Our Vacuum Casting 3D Printing technology has revolutionized the way companies manufacture products," said [Company Spokesperson]. "We are proud to be helping businesses break free from the limitations of traditional manufacturing and embrace a more agile and efficient approach. With our expertise and state-of-the-art equipment, we are committed to driving innovation and delivering results that exceed our clients' expectations."The introduction of Vacuum Casting 3D Printing technology by [Company Name] has created ripples in the manufacturing industry. By addressing the limitations of traditional manufacturing methods, this innovative process offers a cost-effective and time-efficient alternative that unlocks new possibilities for product development and production. With such advancements, manufacturers can now bring their ideas to life more easily and faster than ever before, ushering in a new era of manufacturing excellence.
Revolutionizing 3D Printing: A Closer Look at SLS Technology
[News Title]: Groundbreaking 3D Printing Technology Revolutionizes Manufacturing Industry[News Introduction]:In today's constantly evolving technological landscape, traditional manufacturing practices are being challenged by innovative and groundbreaking solutions. The advent of additive manufacturing, popularly known as 3D printing, has disrupted the industry by offering unparalleled efficiency, cost-effectiveness, and design possibilities. One of the frontrunners in this field, an emerging leader, is significantly transforming the way we think about manufacturing. Their innovative SLS printing technology has already begun revolutionizing various sectors by addressing key challenges and offering outstanding solutions.[Company Introduction]:The pioneering company, leveraging state-of-the-art manufacturing techniques and an impeccable understanding of industry needs, has emerged as an industry trailblazer. Founded on the principles of innovation, sustainability, and affordability, this cutting-edge organization has a track record of consistently pushing the boundaries of what is possible. Their SLS printing technology has gained widespread acclaim and recognition for its ability to transform complex designs into physical objects with stunning accuracy.[Background]:Traditional manufacturing processes often encounter limitations when it comes to creating intricate or customized designs. Conventional methods, such as injection molding or subtractive manufacturing, are time-consuming and costly. Prototyping and production can be resource-intensive, and the limitations tied to these techniques often hamper innovation and creativity. However, with the introduction of SLS printing, the game is set to change.[SLS Printing Revolutionizing Manufacturing]:SLS printing, short for Selective Laser Sintering, boasts several advantages over traditional manufacturing processes. Using powdered materials, such as plastics, metals, or ceramics, SLS printing creates three-dimensional objects by selectively fusing the powdered particles layer by layer. This process not only eliminates the need for expensive tooling but also unlocks endless possibilities for design complexity and customization.Furthermore, SLS printing enables the creation of structures with intricate internal geometries, making it ideal for producing lightweight components that would be impossible through traditional means. The technology's ability to print objects with moving parts or integrated functionalities amplifies its potential applications across various industries.In addition to its design flexibility, SLS printing also reduces waste compared to conventional manufacturing methods. By using only the necessary amount of raw material, it minimizes the ecological impact and material waste. Consequently, this groundbreaking technology aligns perfectly with the global shift towards sustainability and eco-friendly practices.[Applications and Impact]:The advent of SLS printing technology opens up exciting opportunities across multiple sectors. In the healthcare industry, medical professionals now have the ability to create custom implants tailored to individual patients, enhancing treatment outcomes and patient satisfaction. The aerospace industry benefits from lightweight yet structurally sound components, improving fuel efficiency and reducing emissions. Automotive manufacturers can now produce complex designs for customized parts and rapid prototyping, reducing production time and costs significantly.Moreover, SLS printing empowers creative designers and artists by translating their intricate visions into physical reality. Artists can now produce sculptures and intricate artworks that were once deemed impossible to fabricate. Architects can design and print detailed scale models, enabling better visualization and collaboration with clients.[Conclusion]:As the manufacturing industry embraces the innovation and potential of SLS printing, the possibilities for growth and development are immense. This revolutionary technology not only enhances design flexibility and efficiency but also contributes to creating a more sustainable and environmentally conscious future. With its continuous efforts in pushing the boundaries of what is possible, the company has established itself as a key player driving the 3D printing revolution. As industries across the globe adopt SLS printing, it can be anticipated that we are witnessing the dawn of a new era in manufacturing.
Unveiling the Latest Innovations and Advancements in CNC Metalworking
CNC Metalworking Continues to Revolutionize the Manufacturing IndustryIn the fast-paced world of manufacturing, precision and efficiency are key. One company has been at the forefront of revolutionizing the industry by utilizing CNC metalworking technology to create high-quality products with speed and accuracy. With their cutting-edge machinery and dedication to innovation, this company is poised to lead the way into the future of manufacturing.Founded in 1995, this company has been a driving force in the CNC metalworking industry for over two decades. With their state-of-the-art facilities and highly skilled technicians, they have been able to consistently deliver exceptional results to their clients. By investing in the latest advancements in CNC machining technology, they have been able to streamline production processes and enhance product quality.One of the biggest advantages of CNC metalworking is its ability to manufacture intricate parts with unparalleled precision. This level of accuracy ensures that each component produced meets the strictest quality standards. Gone are the days of human error and inconsistency. CNC machines can replicate designs with absolute fidelity, resulting in flawless and reliable products every time.Furthermore, CNC metalworking significantly reduces production time. With traditional methods, manufacturing even a simple part could take days or even weeks. However, with the implementation of CNC machinery, the time required to produce complex components has been drastically reduced. This accelerated turnaround time allows businesses to meet consumer demands more efficiently and stay ahead of their competition.The benefits of CNC metalworking extend beyond precision and speed. This manufacturing process also offers a range of material options to choose from. With the ability to work with various metals such as aluminum, stainless steel, and titanium, this company is able to cater to a wide array of industries and their unique requirements. From aerospace to automotive, medical to electronics, their CNC metalworking capabilities are limitless.Additionally, CNC metalworking is highly cost-effective. By automating the production process, this company can minimize labor costs and reduce material waste. With skilled technicians operating the CNC machines, errors are minimized, resulting in fewer defective parts. This not only saves time and money but also ensures that quality standards are consistently met.Furthermore, CNC metalworking eliminates the need for retooling between different jobs. Changing from one product to another in traditional manufacturing often required extensive setup and reconfiguration of the machinery. However, CNC machines can easily switch between jobs without any significant downtime. This flexibility allows for improved efficiency and increased production capacity.In order to stay at the forefront of the CNC metalworking industry, this company continually invests in research and development. By keeping a close eye on emerging technologies and trends, they can adapt and integrate the latest advancements into their production processes. This commitment to innovation ensures that they remain ahead of their competition and continue to offer cutting-edge solutions to their clients.As the manufacturing industry continues to evolve, CNC metalworking will undoubtedly play a crucial role in shaping its future. With its combination of precision, efficiency, and versatility, this technology is revolutionizing the way products are made. This company's dedication to excellence and their adoption of CNC metalworking continues to set new standards in the manufacturing industry.In conclusion, this renowned company has truly made a mark in the CNC metalworking industry. Their commitment to precision, efficiency, and innovation has allowed them to create superior products that meet the demanding requirements of various industries. With their state-of-the-art facilities and highly skilled technicians, they are well-positioned to continue leading the way in CNC metalworking. As the manufacturing industry moves forward, this company's dedication to excellence ensures that they will remain at the forefront of innovation and continue to shape the future of manufacturing.
Boost Your Prototyping Process with Cutting-Edge Custom Solutions
Custom Prototyping, a leading provider of innovative manufacturing solutions, has recently unveiled its latest breakthrough in the world of prototyping. This state-of-the-art technology promises to revolutionize the way prototypes are developed, giving businesses a competitive edge in their respective industries.Founded in 2005, Custom Prototyping has been at the forefront of delivering cutting-edge prototyping solutions to a diverse range of clients. With a team of highly skilled engineers and designers, the company has earned a formidable reputation for its expertise in transforming concepts into tangible prototypes.The newly launched technology marks a major milestone for Custom Prototyping. By integrating advanced additive manufacturing processes with their existing prototyping methods, the company has created a hybrid solution that offers unmatched precision, speed, and cost-effectiveness.One of the key advancements in this breakthrough technology is the use of 3D printing. By leveraging the power of additive manufacturing, Custom Prototyping is able to rapidly create prototypes with intricate details and complex geometries. This not only significantly reduces the time required for traditional manufacturing processes, but also allows for greater design flexibility and customization.The benefits of 3D printing extend beyond just speed and complexity. With this technology, Custom Prototyping is able to produce prototypes using a wide range of materials, including metals, plastics, and even bio-compatible substances. This opens up countless possibilities for businesses operating in various sectors, such as aerospace, automotive, healthcare, and consumer electronics.Moreover, the integration of other cutting-edge technologies, such as CNC machining and rapid tooling, further enhances the efficacy of Custom Prototyping's new solution. By seamlessly combining different manufacturing techniques, the company is able to provide clients with prototypes that closely resemble the final product in terms of both form and functionality.Speaking about the breakthrough, the CEO of Custom Prototyping, John Smith, expressed his excitement about the endless possibilities this technology brings to their clients. He said, "We are thrilled to introduce this game-changing technology to the market. Our aim has always been to empower businesses with the tools they need to stay ahead in a rapidly evolving industrial landscape. With this new solution, we believe we have achieved exactly that."The impact of Custom Prototyping's latest innovation is already being felt across various industries. Companies that have partnered with the company have reported significant improvements in their product development processes. Not only are they able to iterate designs faster, but they are also able to test the functionality and user experience of new products before investing in large-scale production.In addition to the economic benefits, this technology has notable environmental advantages as well. With its ability to minimize material waste through precise and optimized manufacturing, it aligns perfectly with the growing global emphasis on sustainability and minimizing carbon footprints.As businesses increasingly recognize the importance of agility and rapid innovation, Custom Prototyping's new solution arrives at the perfect time. By providing a streamlined prototyping process that reduces time-to-market and fosters rapid iteration, the company is empowering businesses to embrace innovation and reach new heights.Looking towards the future, Custom Prototyping remains committed to pushing the boundaries of what is possible in the world of prototyping. With a strong focus on research and development, the company aims to continue enhancing its solutions to meet the evolving needs of its clients.As more businesses recognize the advantages of incorporating advanced prototyping technologies into their product development processes, partnerships with forward-thinking companies like Custom Prototyping are likely to become increasingly sought after. With its proven track record and commitment to innovation, Custom Prototyping is poised to lead the way in the era of next-generation prototyping.